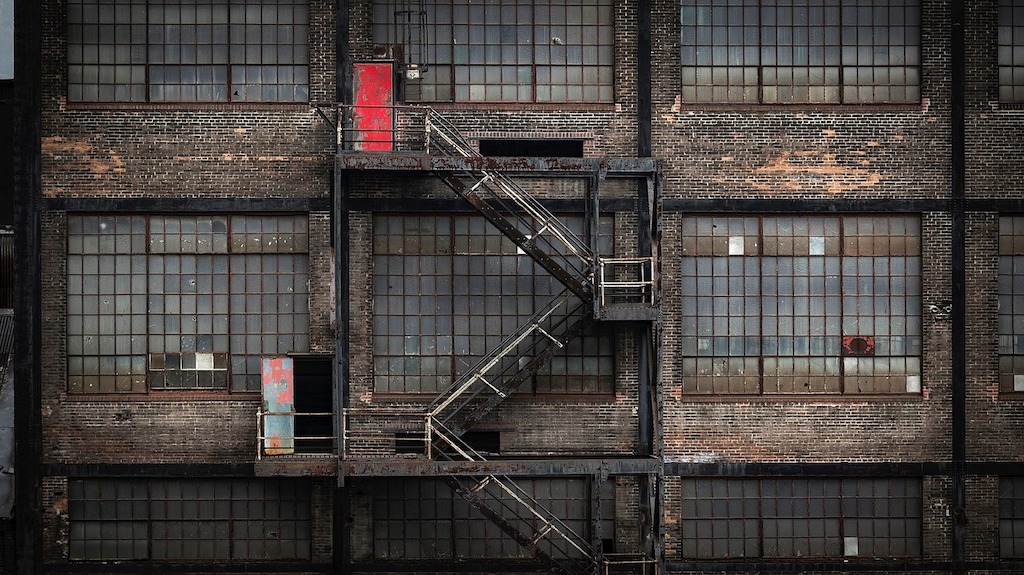
Whether you’re a seasoned veteran or a new hire, prioritizing factory safety is an ongoing commitment. This article is your one-stop shop for essential tips to keep yourself and your fellow workers protected. From mastering the machinery to knowing your escape routes, we’ll cover 10 key practices that can make all the difference.
Click on the links below if you’d like to skip ahead to a section:
Need help with factory safety? ACUTE offers a variety of training courses that can help! With over 200 years of combined experience, our instructors can teach you and your employees how to keep your workplace safe!
Contact ACUTE today to learn more about what we offer.
1. Master the Machine
One of the biggest parts of factory safety is knowing how to properly operate any machinery that you might be using.
In any factory setting, operating machinery safely and efficiently is paramount. Here’s why knowing how to operate machinery properly is so important:
Safety First:
- Reduced Risk of Accidents: Proper training equips workers with the knowledge and skills to identify and avoid potential hazards associated with machinery operations. This significantly reduces the risk of accidents, injuries, and even fatalities.
- Emergency Preparedness: Understanding the machinery’s functions allows for a quicker and more effective response in case of malfunctions or emergencies. Workers can take appropriate actions to shut down equipment safely and minimize damage.
Increased Efficiency and Productivity:
- Optimal Performance: Knowing how to operate machinery correctly ensures it functions at its peak capacity. This leads to higher-quality output and avoids production delays caused by improper use.
- Reduced Downtime: Trained operators can identify minor issues and perform basic troubleshooting, minimizing downtime caused by waiting for maintenance personnel.
- Multitasking and Versatility: Cross-trained workers who can operate multiple machines offer greater flexibility in production schedules and can adapt to changing demands more efficiently.
Protecting Equipment and Assets:
- Minimised Wear and Tear: Operating machinery according to manufacturer guidelines extends its lifespan and reduces the need for costly repairs or replacements.
- Reduced Risk of Damage: Improper use can lead to equipment malfunctions, breakdowns, and even damage to materials and finished products.
Overall Workplace Benefits:
- Improved Morale: A safe and efficient work environment fosters a sense of confidence and well-being among workers.
- Reduced Costs: The benefits of safe and proper machinery operation translate to lower insurance premiums, less downtime, and increased production.
- Enhanced Company Reputation: A commitment to worker safety and proper training demonstrates a company’s dedication to responsible practices, which can positively impact its reputation.
In conclusion, knowing how to operate machinery properly goes far beyond just completing tasks. It’s a cornerstone of a safe, productive, and efficient factory environment. By prioritizing proper training and ensuring workers are comfortable and knowledgeable about the equipment they operate, everyone benefits – workers, companies, and ultimately, the quality of the products produced.
Before operating any equipment, ensure that all employees have received proper training and understand all safety protocols.
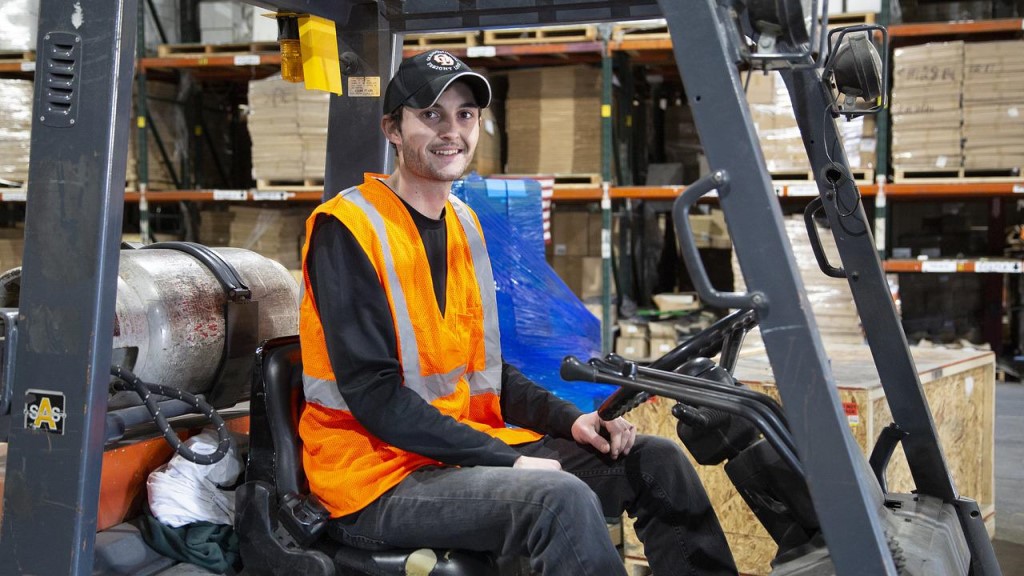
2. Know Your Escape Routes
Factory fires are a serious threat, but having a plan can make all the difference for factory safety. Here’s why knowing your escape routes is crucial:
- Think Fast, Act Faster: In the event of a fire, every second counts. Being familiar with multiple escape routes allows you to react quickly and choose the safest path out, even if smoke or flames block your primary exit.
- Stay Calm, Lead the Way: Knowing the evacuation procedures empowers you to guide others, especially new employees or those unfamiliar with the layout. Being a fire safety champion can ensure everyone gets out safely.
- Practice Makes Perfect: Don’t wait for a real fire! Participate in fire drills regularly. This helps you become comfortable with the evacuation process, identify any potential obstacles, and ensure a smooth and efficient evacuation in case of an emergency.
Remember, a few minutes spent familiarizing yourself with fire exits and evacuation procedures could save your life and the lives of your colleagues. Don’t be caught off guard – be prepared!
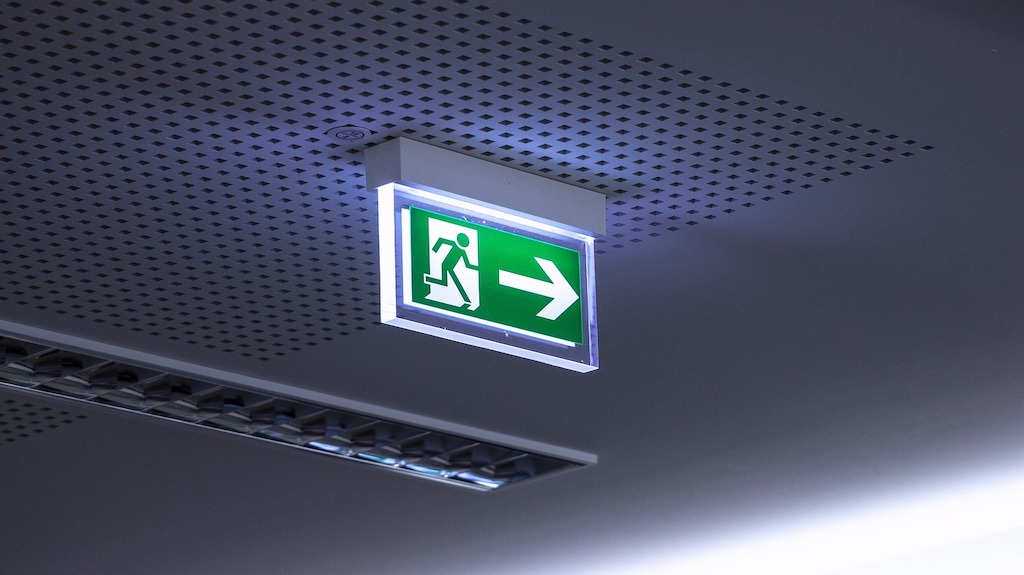
3. Stay Sharp, Stay Safe
The factory floor can involve a variety of materials, some with potential hazards. That’s why the Workplace Hazardous Materials Information System (WHMIS) is so important. But WHMIS knowledge isn’t a one-time deal! Here’s why keeping your WHMIS certification current is crucial:
- Safety First, Always: WHMIS regulations are constantly evolving to reflect new information and best practices for handling hazardous materials. Renewing your certification ensures you have the most up-to-date knowledge to protect yourself and your colleagues.
- Knowing the Risks: WHMIS training equips you to identify potential hazards associated with different materials, understand the proper handling procedures, and recognize the safety symbols and labels used on containers. Keeping this knowledge fresh allows you to make informed decisions and avoid accidents.
- Employer Expectations: Most employers require WHMIS certification for workers who may encounter hazardous materials. Staying current demonstrates your commitment to workplace safety and fulfills your job requirements.
Think of WHMIS renewal as a safety shield upgrade!
By refreshing your knowledge, you’re strengthening your ability to work safely and contribute to a positive safety culture in your factory. So, check your certification expiry date and don’t hesitate to ask your supervisor or HR department about renewal options. Remember, safety is a continuous journey, and WHMIS updates are your map to a safe and healthy work environment.
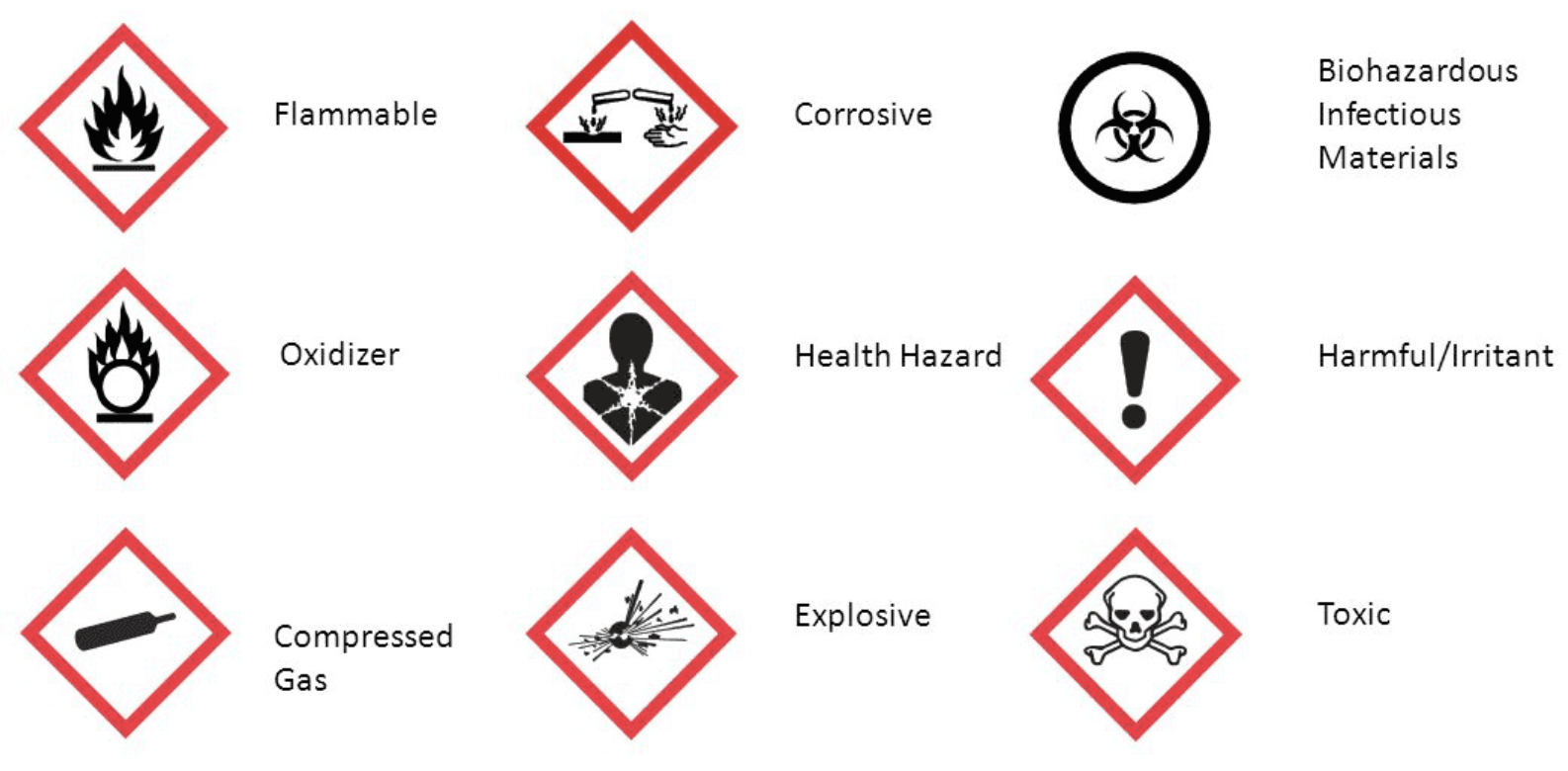
4. Clear the Way
A busy factory floor can get cluttered fast. But amidst the hustle and bustle, one thing should always be a priority for factory safety: clear and unobstructed walkways and work areas. Here’s why:
- Trip Hazards Be Gone: Clutter creates tripping hazards, which are a leading cause of workplace injuries. Keeping walkways clear minimizes the risk of slips, falls, and potential injuries that can disrupt production and cause delays.
- Safety on the Move: Unobstructed walkways ensure smooth and efficient movement of people and materials throughout the factory. This reduces congestion, allows for quick access to equipment and emergency exits, and fosters a more organized work environment.
- Maintaining the Flow: A clear workspace promotes better workflow. Workers can easily access tools, materials, and equipment they need, minimizing wasted time and frustration caused by blocked passageways.
See Something, Say Something (Safely!)
If you ever encounter blocked walkways or cluttered work areas, don’t hesitate to report it to your supervisor or a designated safety representative. A quick heads-up can prevent potential accidents and ensure everyone can move around the factory floor safely.
Remember: A clean and organized workspace is a safe workspace. By keeping walkways clear and reporting any obstructions, you’re actively contributing to a safer and more efficient work environment for yourself and your fellow workers.
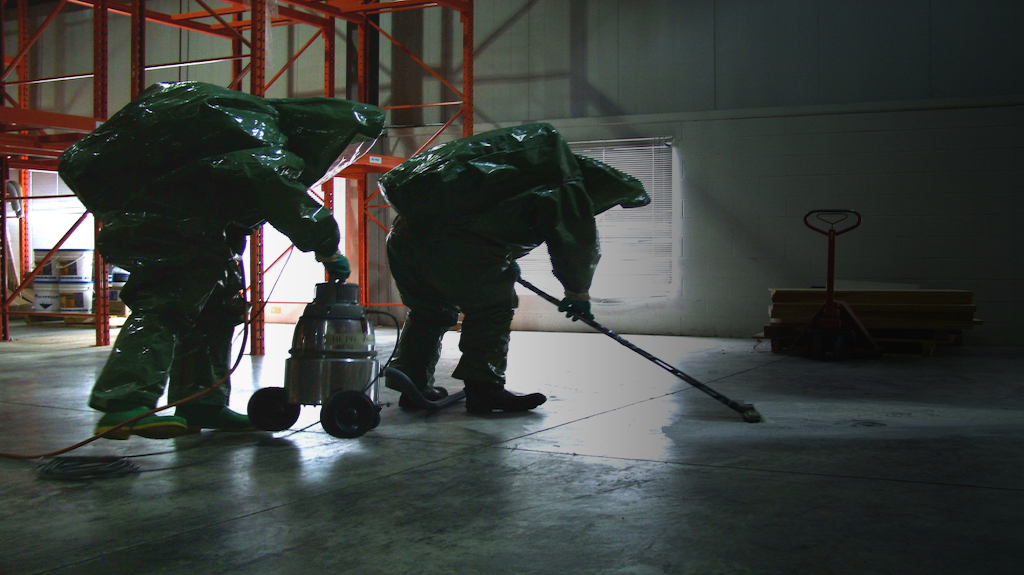
5. Ergonomics Matter
Working long hours on a factory floor can take a toll on your body. That’s where ergonomics comes in! Here’s why requesting an ergonomic assessment of your workstation is a smart move:
- Your Body Matters: Repetitive motions, awkward postures, and uncomfortable workstations can lead to musculoskeletal disorders (MSDs) like carpal tunnel syndrome or back pain. An ergonomic assessment identifies potential risk factors in your work environment and helps adjust them to promote proper posture and reduce strain.
- Prevention is Key: Catching ergonomic issues early can prevent them from turning into serious injuries that require extensive treatment and time off work. An assessment helps nip potential problems in the bud and keep you healthy and productive.
- A More Comfortable You, a More Productive You: Working in a comfortable and ergonomic environment reduces fatigue and discomfort, leading to increased focus and improved productivity. You’ll feel better and get more done throughout your shift.
- It’s Your Right! Most provinces, including Ontario, have regulations that require employers to provide ergonomically sound work environments. Don’t hesitate to request an assessment – it’s your right to work in a safe and healthy environment.
Ergonomics is all about creating a work environment that works for you, not against you.
By requesting an ergonomic assessment, you’re taking a proactive approach to protecting your health and well-being. Don’t be afraid to speak up! A comfortable and properly adjusted workstation can make a world of difference on the factory floor.
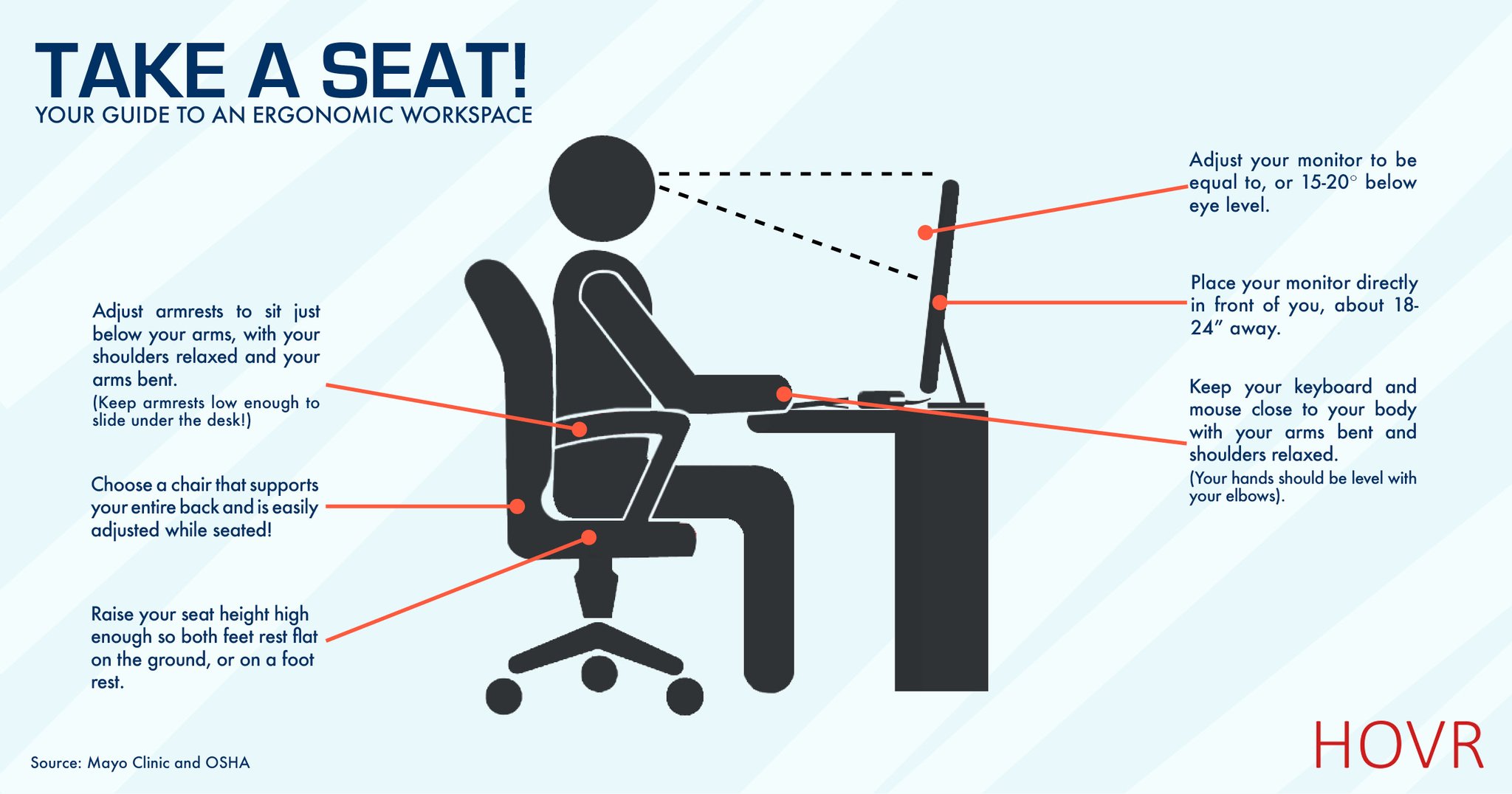
6. Keep Out the Unqualified
Factory safety depends on everyone playing their part. One crucial aspect is keeping unauthorized personnel out of restricted areas. Here’s why your vigilance matters:
- Safety First: Restricted areas often contain hazardous materials, complex machinery, or ongoing processes. Untrained or unauthorized personnel entering these zones risk serious injuries to themselves and others.
- Following Procedures: Restricted areas exist for a reason. They have specific safety protocols and procedures in place to minimize risks. The presence of unauthorized personnel disrupts these procedures and can lead to accidents.
- Protecting Equipment: Machinery in restricted areas is often delicate and requires specialized knowledge to operate safely. Untrained individuals attempting to use such equipment can damage it, leading to costly repairs and production delays.
- Be the Eyes and Ears: If you see someone entering a restricted area who shouldn’t be there, report it immediately. Your vigilance can prevent accidents and ensure everyone’s safety.
Here’s what you can do:
- Know Your Boundaries: Be familiar with the layout of the factory and understand which areas are restricted.
- See Something, Say Something: If you see someone entering a restricted area without proper authorization, politely but firmly inform them it’s off-limits and report it to your supervisor or security personnel.
- Be a Safety Champion: Encourage your colleagues to be aware of restricted areas and the importance of following safety protocols.
Remember, a safe factory is a successful factory. By being a gatekeeper for restricted areas and reporting unauthorized access, you’re playing a vital role in ensuring everyone’s well-being and a smooth-running operation.
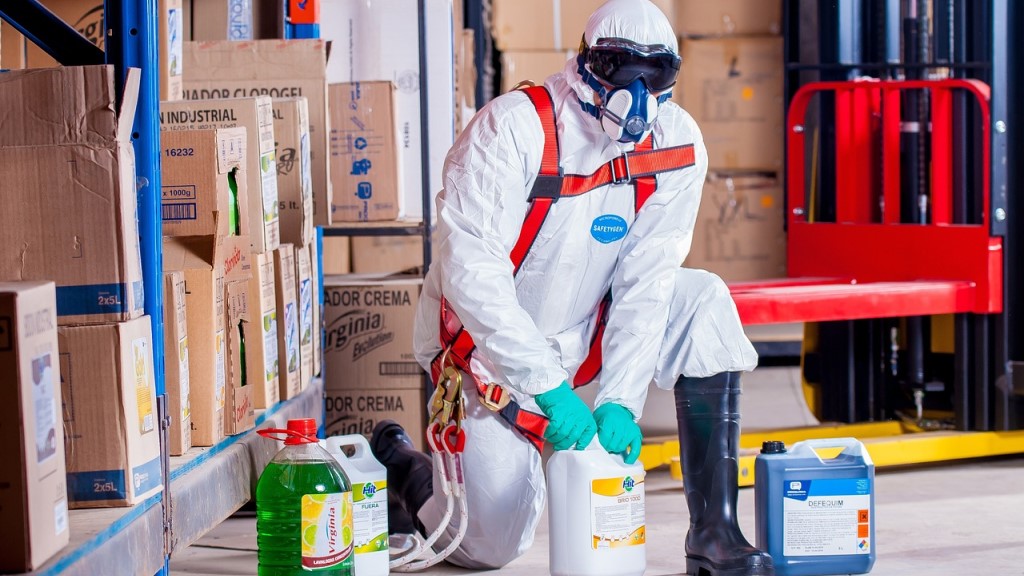
7. Safety Supervisor: Your Ally
The factory floor can be a complex environment, but you don’t have to navigate it alone. Your health and safety supervisor is there to be your champion! Here’s why actively collaborating with them is essential:
They’re Here for You:
Health and safety supervisors are not there to be the “fun police.” Their primary role is to protect you and your colleagues. They have the expertise and knowledge to identify and address potential hazards, ensuring a safe work environment for everyone.
Listen Up, Stay Safe:
Actively listening to their instructions is crucial. They’ll provide safety briefings, explain proper procedures, and outline any potential risks associated with specific tasks. Their words can make all the difference in preventing accidents.
See Something, Say Something (Safely!):
If you observe a safety hazard – a malfunctioning machine, a blocked walkway, or anything else that seems off – don’t hesitate to report it to your supervisor. They can address the issue promptly and prevent potential injuries.
Never Be Afraid to Ask:
Feeling unsure about a task or safety protocol? Ask questions! There are no dumb questions when it comes to safety. Your supervisor is there to guide you and ensure you have the knowledge and confidence to perform your job safely.
Building a Safety Culture Together:
By actively collaborating with your health and safety supervisor, you’re not just protecting yourself, you’re contributing to a positive safety culture within the factory. This collaborative approach leads to a safer and healthier work environment for everyone.
Remember: Your health and safety supervisor is your ally, not your adversary. Work together to make the factory floor a safe and productive space for all!
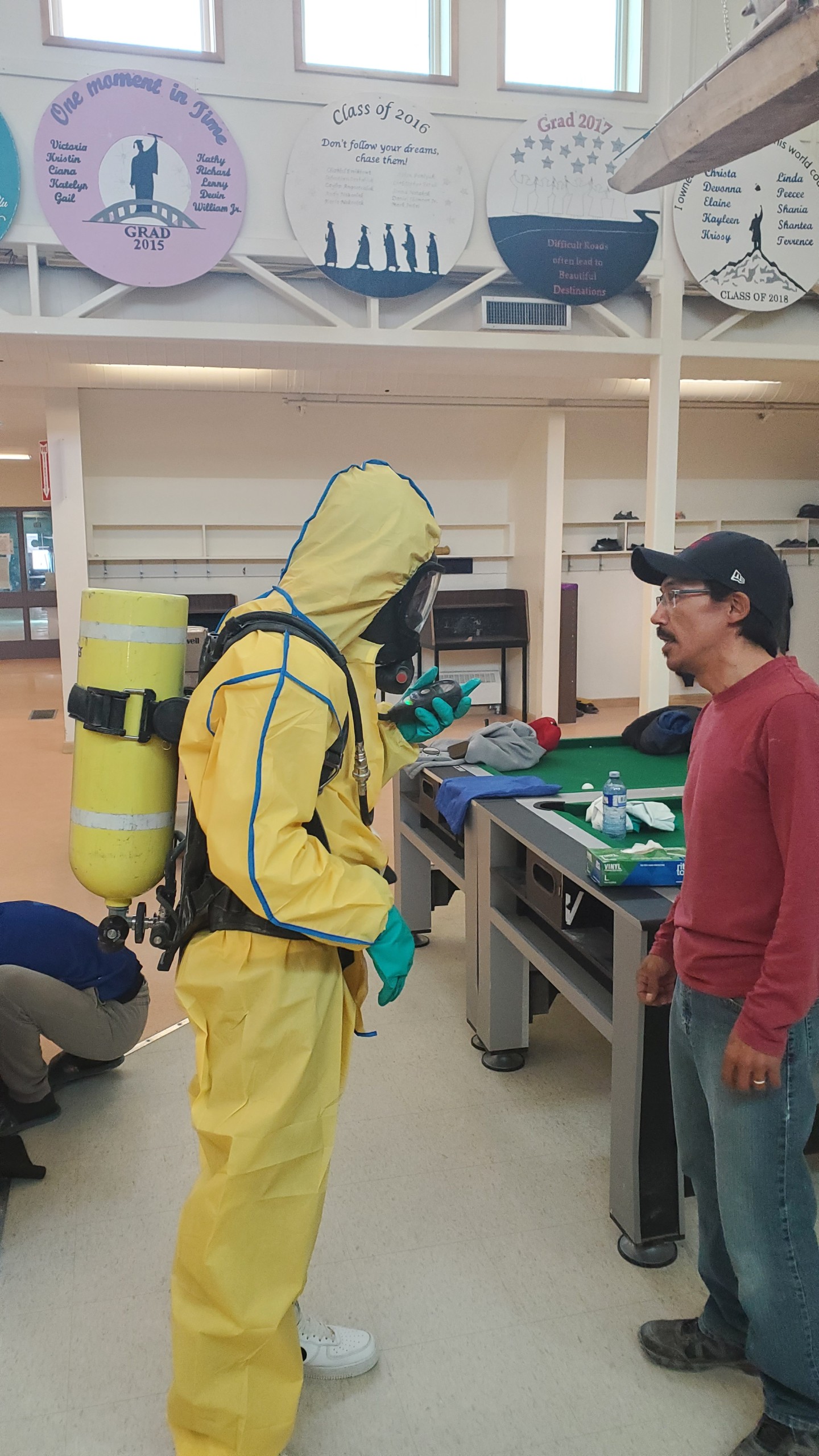
8. Know Your Safety Data Sheets (SDS)
Factory work can involve a variety of materials, some with hidden dangers. That’s where Safety Data Sheets (SDS) come in! Think of them as instruction manuals for hazardous materials, but way more important. Here’s why ensuring readily available SDS are crucial:
- Knowledge is Power (and Protection): SDS contains vital information on the properties of hazardous materials, potential health risks, safe handling procedures, and proper storage guidelines. By understanding these details, you can protect yourself from accidents and exposure.
- Emergency Action Plan: In case of an accidental spill, leak, or exposure, the SDS outlines critical emergency procedures. Knowing the appropriate steps to take can minimize damage, prevent injuries, and ensure a swift and effective response.
- The Right Gear for the Job: The SDS specifies the recommended Personal Protective Equipment (PPE) needed when handling specific materials. This could include gloves, goggles, respirators, or other safety gear. Knowing the right PPE to use helps shield you from potential hazards.
- Your Right to Know: Having access to SDS is not just a good practice, it’s your legal right as a worker! Don’t hesitate to ask your supervisor for the SDS for any material you’re unsure about.
Here’s what you can do:
- Location, Location, Location: Ensure SDS are readily available in a designated location near where hazardous materials are used or stored. This allows for quick access in case of an emergency.
- Ask and Learn: If you can’t find the SDS or have questions about a specific material, don’t be shy! Ask your supervisor or a designated safety representative for clarification.
Remember: SDS is your lifeline when dealing with hazardous materials. By ensuring they’re readily available and familiarizing yourself with their contents, you’re taking a proactive approach to safety and protecting yourself from potential harm.
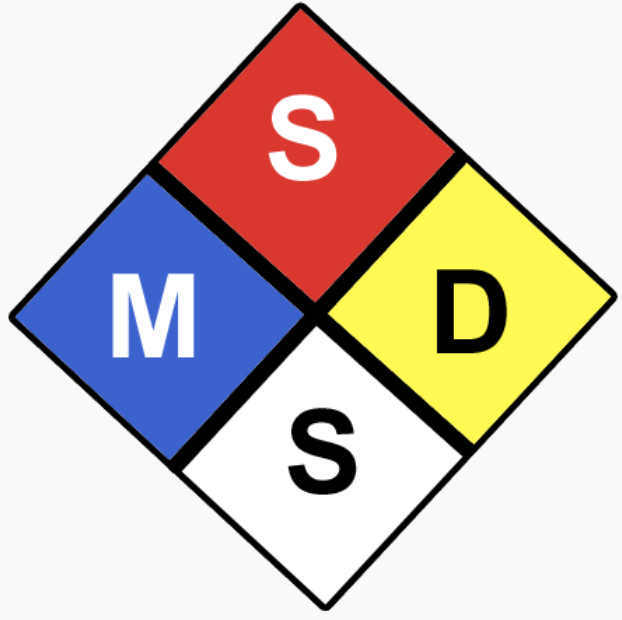
9. Report All Injuries
Accidents happen, even in the most controlled environments. But when they do, it’s crucial to take every injury seriously. Here’s why reporting even seemingly minor injuries to your supervisor is essential:
- Early Intervention is Key: A minor injury, like a cut or a sprain, might seem insignificant at first. However, if left untreated, it could develop into a more serious problem. Reporting it early allows for proper evaluation and treatment, preventing potential complications and ensuring a faster recovery.
- Documentation is Your Shield: Properly documenting an injury creates an official record of the incident. This can be crucial if you require future medical attention or need to file a Workplace Safety and Insurance Board (WSIB) claim.
- Identifying Trends: Reporting minor injuries helps identify potential safety hazards in the workplace. By tracking these incidents, employers can take proactive steps to prevent similar accidents from happening in the future.
- Building a Culture of Safety: When injuries are reported consistently, it fosters a culture of safety within the factory. This encourages everyone to prioritize safety and be more aware of potential risks.
Here’s what you can do:
- Report It, Don’t Ignore It: No matter how minor you think an injury is, report it to your supervisor immediately. They can assess the situation and determine the necessary course of action.
- Details Matter: Provide a clear description of the injury, how it happened, and any initial symptoms you’re experiencing. This information helps ensure you receive appropriate medical attention.
- Seek Medical Attention: If your supervisor recommends it, or if you feel any discomfort, don’t hesitate to seek medical attention. Early treatment can significantly improve your recovery time.
Remember: Every injury deserves attention. By reporting even seemingly minor incidents, you’re prioritizing your health, contributing to a safer workplace, and ensuring you receive the proper care you need to get back on your feet quickly.
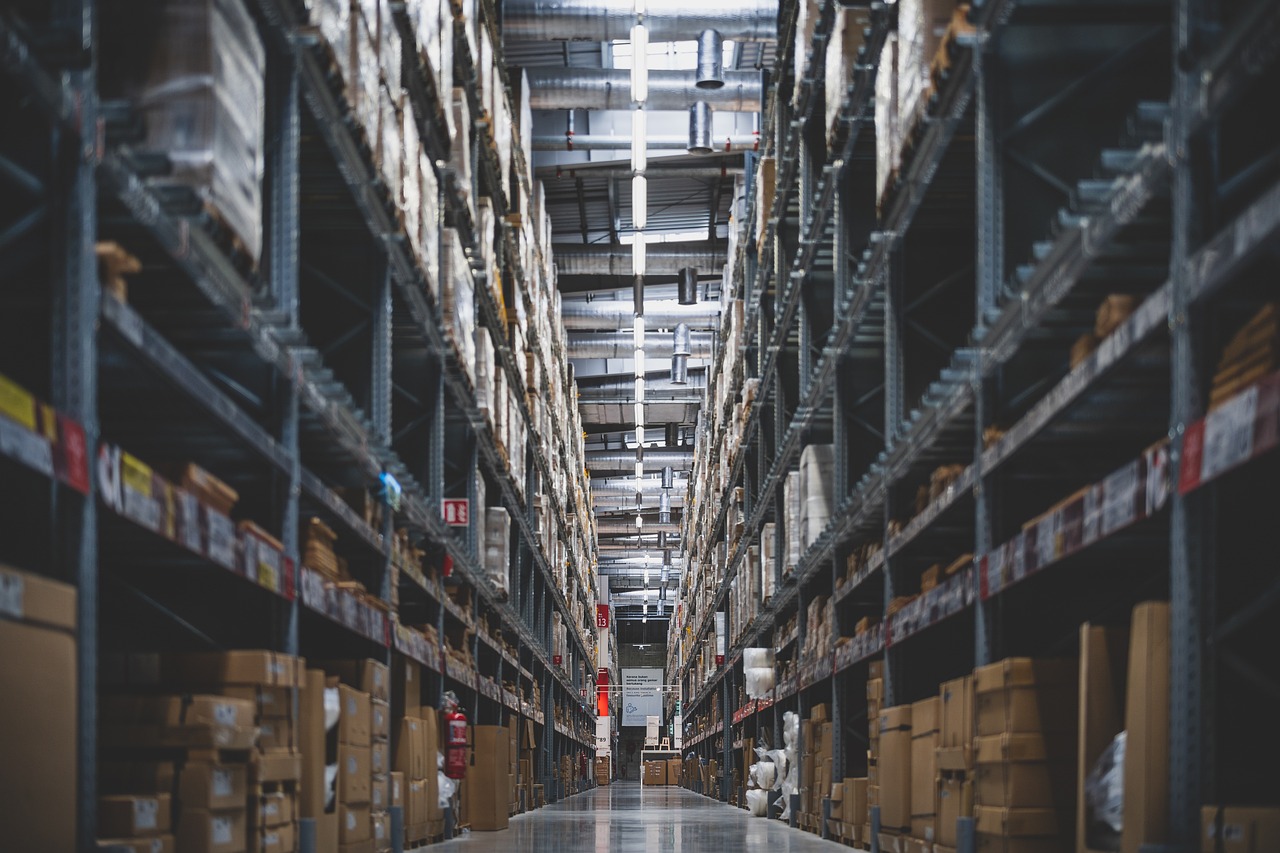
10. Speak Up, Stay Safe
Factory safety is the cornerstone of any successful factory operation. But creating a truly safe environment requires everyone’s participation. Here’s why speaking up about unsafe work practices is not just your right, it’s your responsibility:
- Your Safety, Your Priority: No task is worth risking your health or well-being. If you see something unsafe, like bypassing safety protocols or using faulty equipment, don’t hesitate to speak up. Your voice can prevent accidents and protect yourself and your colleagues.
- Don’t Be Pressured into Risk: Sometimes, production pressures might lead to shortcuts or ignoring safety procedures. Refuse to perform tasks that you feel are unsafe. Your supervisor and colleagues will respect your decision to prioritize safety.
- Building a Safety Culture: Speaking up about unsafe practices sets a positive example for others. It encourages open communication about safety concerns and fosters a culture where everyone feels empowered to prioritize safety over shortcuts.
- Empowerment Through Knowledge: Don’t be afraid to ask questions! If you’re unsure about a task or a safety procedure, speak up and ask for clarification. Understanding proper procedures is key to avoiding accidents.
- You’re Not Alone: Most factories have clear channels for reporting safety concerns. Talk to your supervisor, a health and safety representative, or a designated safety committee member. They will take your concerns seriously and address them appropriately.
Remember: Your voice matters! Speaking up about unsafe practices is not snitching, it’s safety leadership. By taking a stand, you’re creating a safer work environment for everyone, and that’s something to be proud of.
So, the next time you see something unsafe, don’t be a bystander. Speak up and be a champion for safety on the factory floor!

Invest in Factory Safety, Invest in Success: Why Choose ACUTE Safety?
At ACUTE Safety, we go beyond just checking the box for safety training. Here’s why partnering with ACUTE is the smart choice for your company:
1. Open Door Learning: Forget one-size-fits-all lectures. Our instructors foster an open environment where questions and concerns are welcomed. We believe in a collaborative learning approach that ensures your team gets the most out of every training session.
2. Industry Expertise, Across the Board: We’ve trained teams in manufacturing, construction, healthcare, education, and government. This vast experience allows us to bring best practices from all sectors to your specific industry, ensuring your training is relevant and impactful.
3. Real-World Solutions, Not Theory: Our instructors have over 100 years of combined experience. They don’t just teach safety regulations; they offer practical solutions that can be implemented immediately.
4. Proven Results: Don’t just take our word for it! Our clients rave about our training, giving us a stellar 4.9 out of 5 stars on Google reviews.
ACUTE Safety is more than just training. We’re your partner in creating a safe and successful work environment.
Contact us today to learn how ACUTE can help your team achieve its safety goals.