Surprise inspections can happen at any time — and in Ontario, they’re a key tool used by the Ministry of Labour, Immigration, Training and Skills Development (MLITSD) to evaluate whether workplaces are following the Occupational Health and Safety Act (OHSA). These unannounced visits are meant to catch a snapshot of real working conditions, and they can carry serious consequences if your workplace isn’t up to code.
In this post, we’ll explore what safety inspectors look for during these visits, the most common issues they uncover, what documentation they expect, and how you can stay inspection-ready all year round.
Click on the following sections to learn more.
- Why Surprise Inspections Happen
- What Safety Inspectors Look For
- Common Violations and Risk Areas
- Required Documentation
- How to Stay Inspection-Ready Year-Round
For more on what safety inspectors look for, contact us.
1. Why Surprise Inspections Happen
Surprise workplace inspections in Ontario are conducted by Occupational Health and Safety (OHS) inspectors from the Ministry of Labour, Immigration, Training and Skills Development (MLITSD). These provincial officers are authorized under the Occupational Health and Safety Act (OHSA) to enter and inspect any workplace without advance notice, during regular working hours, and even after hours if needed.
The purpose of these inspections is to ensure employers are following the law, protecting workers, and maintaining a safe working environment. They are not random acts of enforcement, but part of a structured compliance strategy.
Surprise inspections typically fall into one of four categories:
1. Complaint-Based Inspections
If a worker, union, or member of the public files a complaint about unsafe conditions, an inspector may be dispatched to investigate without warning. These complaints are confidential, and the inspector will not reveal the identity of the complainant.
2. Critical Injury or Fatality Response
When a serious injury or death occurs at a workplace, it must be reported to the MLITSD immediately. Inspectors will often arrive on-site within hours to assess what happened, issue any necessary stop-work orders, and determine if the OHSA was violated.
3. Follow-Up on Previous Violations
If a business was previously found to be non-compliant, the inspector may return unannounced to verify whether corrective actions were taken. Repeat violations often lead to more serious enforcement, including fines or prosecution.
4. Sector-Specific Blitzes
The MLITSD routinely conducts inspection blitzes and initiatives targeting specific hazards or industries based on historical injury data. For example, construction sites may be targeted for fall protection enforcement in spring, or warehouses may be checked for machine guarding issues in the fall. These blitzes are announced publicly in advance (via Ontario.ca), but individual site visits are not.
Industries frequently targeted include:
-
Construction – due to high injury rates and fall hazards
-
Healthcare – including hospitals and long-term care homes, where violence prevention is a focus
-
Manufacturing – for equipment safety, PPE use, and chemical handling
-
Warehousing and logistics – for forklift safety, material handling, and ergonomics
The overall goal of these inspections is not to punish employers but to protect workers and promote a culture of proactive compliance. However, if an inspector finds violations — especially those posing immediate danger — they are empowered to issue:
-
Compliance orders, requiring the employer to fix the issue within a deadline
-
Stop-work orders, halting part or all of the workplace activity until the hazard is addressed
-
Tickets or fines, which can range from hundreds to thousands of dollars per violation
Understanding who performs these inspections and why they happen is the first step in ensuring your workplace stays compliant — even when no one is watching.
2. What Safety Inspectors Look For
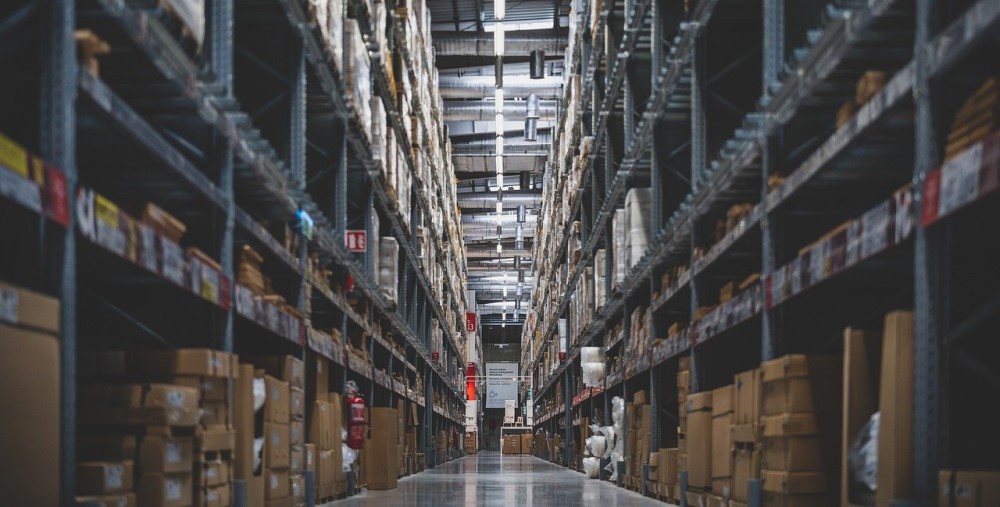
During a surprise inspection, safety officers examine both the physical work environment and the systems in place to support safety. One of the first things they assess is the presence of visible hazards, such as unguarded equipment, blocked emergency exits, fall risks, or improperly stored hazardous materials.
Inspectors also review whether the employer has appropriate policies for workplace violence and harassment. These policies must be written, reviewed annually, and supported by training and a clear procedure for reporting and investigating complaints. Lack of these documents is a common violation.
Employee training and supervision are also closely examined. Inspectors often ask if workers are trained for the tasks they’re performing, and if supervisors are ensuring safety practices are followed. For example, they’ll look for training on WHMIS 2015, Working at Heights (if applicable), and general health and safety awareness.
In addition, they will assess your Joint Health and Safety Committee (JHSC) or Health and Safety Representative, depending on the size of your workplace. Are regular inspections being completed? Are meeting minutes recorded and accessible? Are certified members in place?
Finally, they’ll check whether tools and machinery are being maintained properly. This includes reviewing service logs, checking certifications on lifting equipment, and ensuring safe operating procedures are followed.
3. Common Violations and Risk Areas
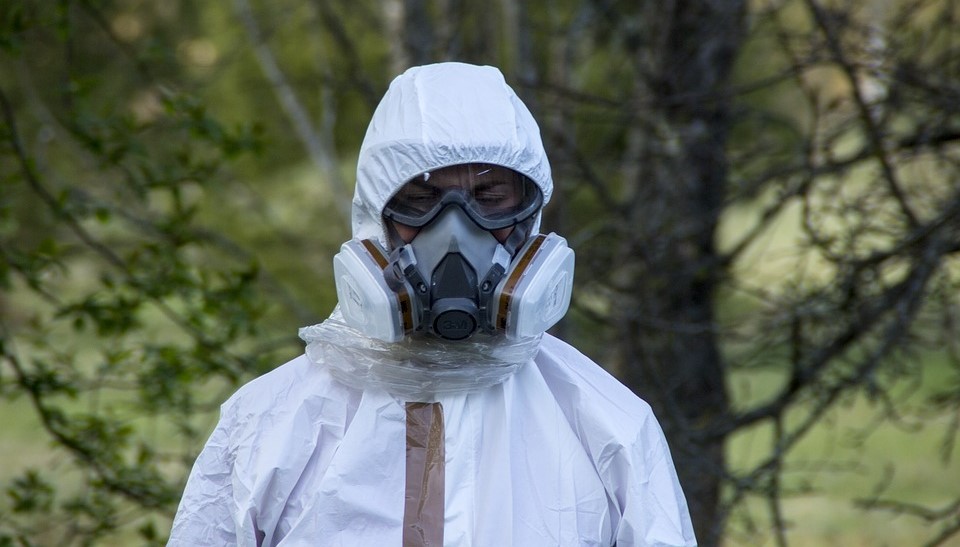
While every inspection is different, certain violations show up time and again. Inadequate or missing personal protective equipment (PPE) is a frequent issue, either because it hasn’t been provided or workers aren’t wearing it. Inspectors also routinely find outdated or missing health and safety policies, especially around violence and harassment.
Improper storage of materials, blocked pathways, and poor housekeeping are also red flags. These seemingly minor issues can pose serious safety risks and may lead to fines or stop-work orders. Another recurring problem is a lack of documented training, especially when new workers haven’t been properly onboarded.
Equipment that hasn’t been maintained or is used unsafely can result in immediate orders to stop using it until repairs are made or procedures corrected. And if fall protection is required but not in place, enforcement actions happen quickly, often on the spot.
4. Required Documentation
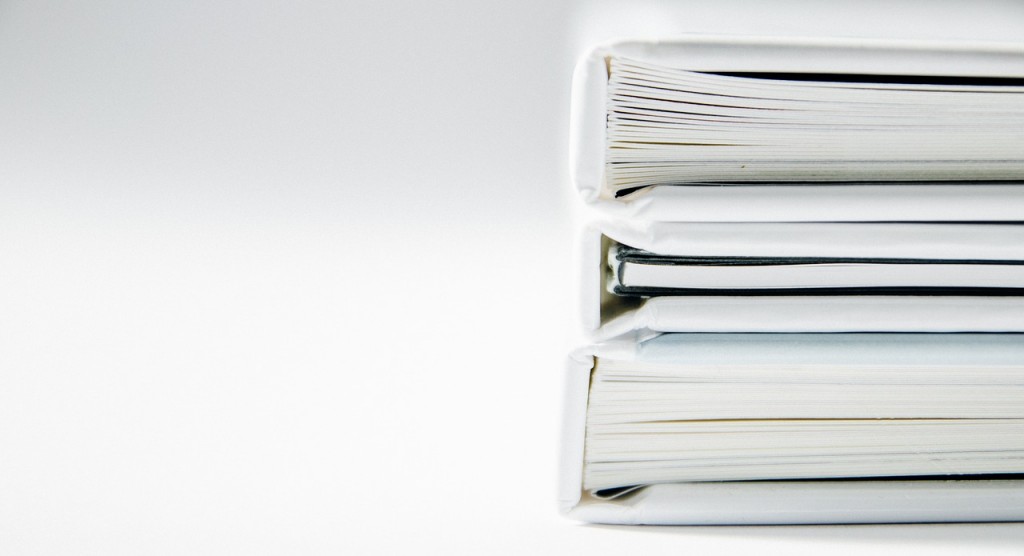
During a visit, inspectors will often request to review your safety documentation.
This may include your company’s health and safety policy (signed and reviewed annually), your workplace violence and harassment policies, and training records for all staff.
They may also want to see maintenance logs for equipment, minutes from JHSC meetings, incident and injury reports, and documentation of workplace inspections or hazard assessments. If your workplace uses hazardous materials, expect a review of WHMIS labels and Safety Data Sheets.
Having these materials easily accessible, clearly organized, and up to date shows that safety is a priority and helps speed up the inspection process.
5. How to Stay Inspection-Ready Year-Round
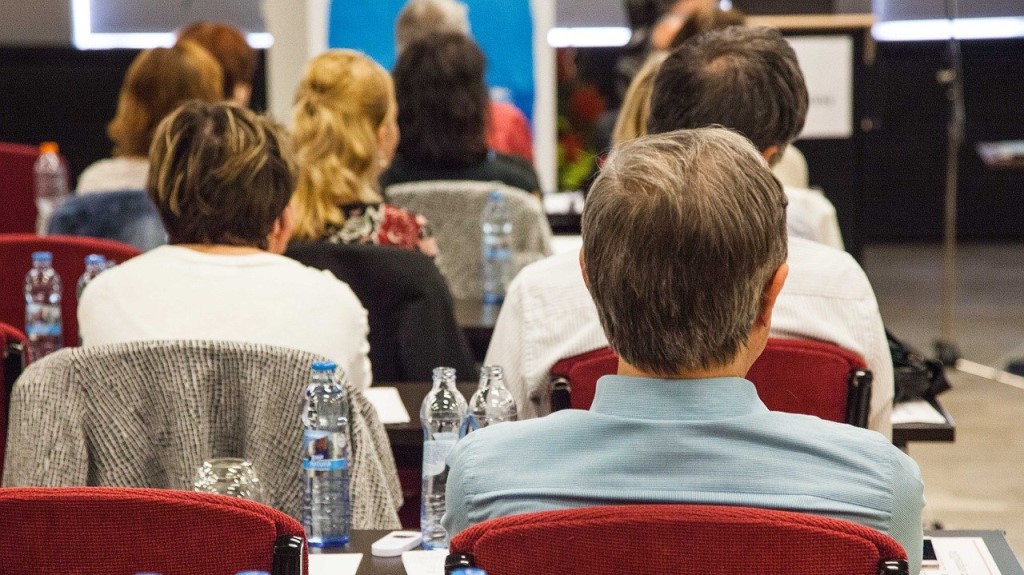
The best way to prepare for a surprise inspection is to never need to prepare at all. That means embedding safety into your day-to-day operations.
Hold regular internal inspections to catch and correct hazards early. Make sure all new employees go through safety orientation, and provide refresher training for existing staff as needed.
Review your policies each year — especially if your team has grown or processes have changed. Encourage your workers to report near-misses and safety concerns so they can be addressed before they become incidents. And ensure your JHSC or Health and Safety Rep is active and engaged in workplace safety.
You don’t need a large team or expensive consultants to build a strong safety culture — just commitment, consistency, and follow-through.
Knowing what safety inspectors look for is about more than passing an inspection — it’s about protecting your people and your business. When safety is treated as a core value rather than a box to check, everyone benefits. You’ll reduce injuries, avoid costly fines, and create a more positive workplace culture.
If you’re unsure where to start, consider reaching out to a certified health and safety consultant or exploring free tools and resources from the Ontario Ministry of Labour.
ACUTE provides comprehensive health and safety training, on-site safety services, and consulting services.
- Extensive Experience: With over 100 years of combined on-site experience, company staff offer more than theoretical abstracts.
- First-Rate Trainers: Our trainers have first-hand experience with what they are training and provide an engaging and fun hands-on teaching approach.
- Tailored Training Solutions: ACUTE offers solutions that are tailored to each customer’s specific applications, company policies, and internal procedures.
- Convenient Location: Based in Waterloo, we proudly serve all of Ontario and have provided services coast to coast.
- World-Class Facility: For many clients, travelling to ACUTE to use one of Canada’s best workplace health and safety training centres is well worth the trip!
What Our Customers Are Saying…
Acute is recognized and respected as a people organization and they have been doing it right for a long time.
Acute has been a staple in supporting my companies over the years and have always delivered quality amd dependable service. Training programs are top shelf and a great facility for practical application. couldn’t recomend them more. keep up the great work folks.
We were referred to ACUTE on behalf of our employer for an n95 mask fitting – the staff here are professional, personable, and informative.
I’d come back here for any safety-related training in a heartbeat.