Does safety training impact production and productivity? Yes, it does, but in a very positive way. Click on each section to learn more.
- How Does Safety Training Impact Production and Productivity?
- How Does a Lack of or Inadequate Safety Training Impact Production?
- How a Joint Health and Safety Committee Can help Improve Productivity
- How to Get Safety Training Without Interrupting Production
If you are looking for professional health and safety training that can be customized to suit your needs, contact us.
1. How Does Safety Training Impact Production and Productivity?
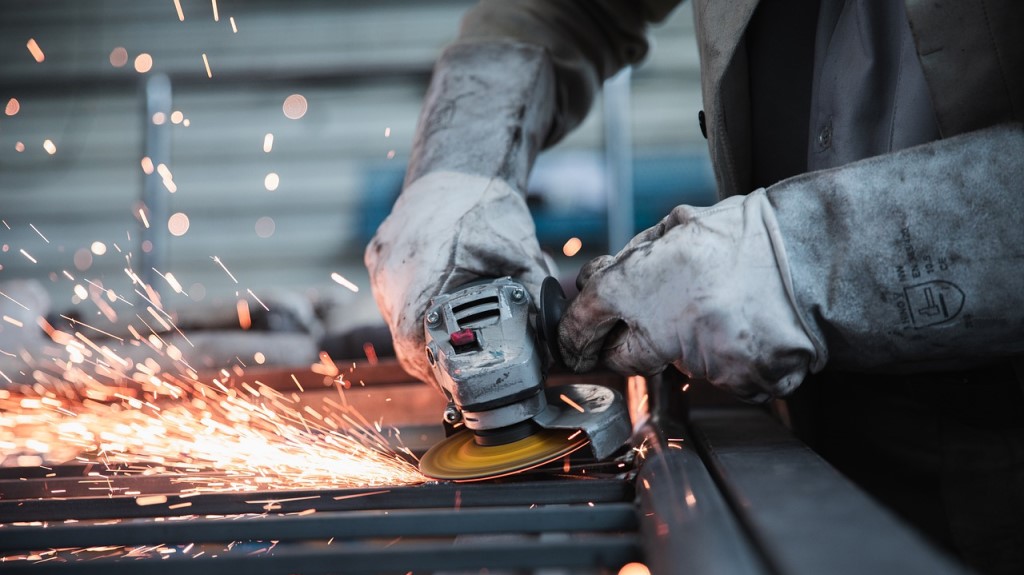
Does safety training impact production? Yes, proper training can improve your productivity and production
Safety training can have a positive impact on production because it help to increase your workers’ productivity. When your workers are properly trained for the work that they are doing, then they will feel confident and less stressed about their tasks.
This is especially true when it comes to safety training. If your workers feel safe doing their job, they will not be stressed about getting injured and hesitant about performing possibly dangerous tasks. Workers who are well-trained can concentrate on the quality of their work instead of worrying about getting injured.
Having a safe work environment will also help to increase worker productivity. Not only is individual safety training important for your workers, but making sure that their worksite is a safe environment is also very important.
Workers need to fee that where they are working is safe too. Some things to consider to make your work environment safe include the following:
- Proper ventilation
- Proper storage of hazardous materials
- Following correct procedures for the transportation of dangerous goods
- Proper lighting
- Eliminating trip and fall hazards
- Having erganomical equipment to use
Having a safe place to work combined with proper safety training will greatly improve your employees’ feeling of security and confidence, thus improving their productivity.
2. How Does a Lack of or Inadequate Safety Training Impact Production?
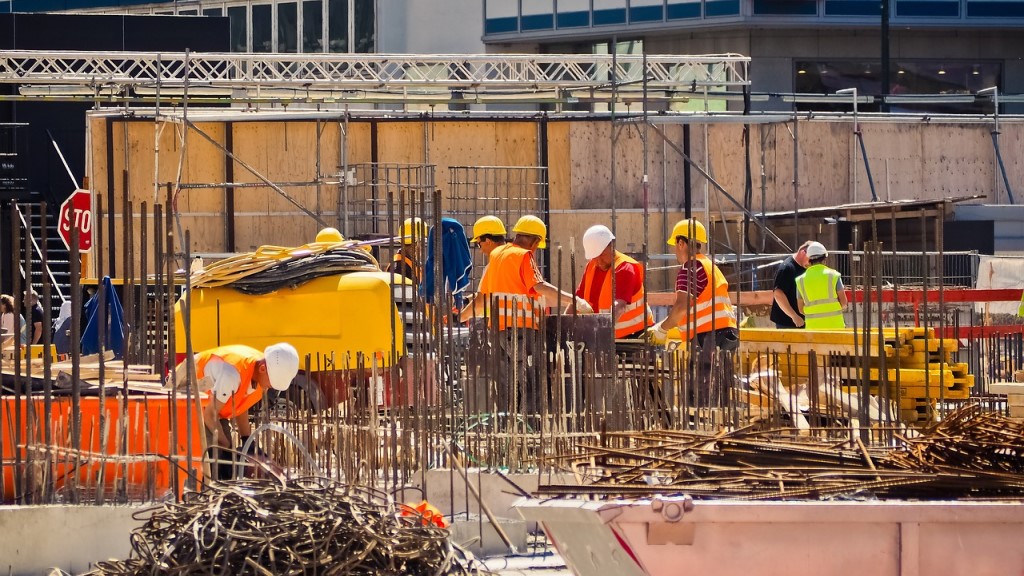
Does inadequate safety training impact production? Yes, with increased downtimes
There are many ways in which a lack of proper safety training or inadequate training can impact production.
Downtime Due to Injuries:
If your workers lack proper safety training, then they are more likely to get injured on the job. If you have workers who need to be off work for a short or extended period of time, this can have a huge impact on your productivity.
If an injury occurs, you may need to hire someone to replace your injured staff. You will need to train new people, which will cost you both time and money.
In the meantime, you may need to work with a smaller number of workers. This will not only decrease your productivity, but it can also affect the morale or your other workers and it can put extra strain and stress on them.
Damage Your Equipment:
Lack of proper safety training will not only jeopardize the health and safety of your workers, but it can also endanger your operations and production.
Equipment or products can be damaged due to accidents, thus reducing your productivity. You may also have to spend money repairing or replacing damaged equipment or products that result from a safety accident.
Fines:
Lack of safety training can also result in fines or litigation. There are many safety training courses that are mandatory, such as Working at Heights training. Non-compliance with these safety training regulations could be extremely costly for your company.
Reputation:
Another negative impact that a lack of safety training can have is that it can give your company a bad reputation. Not only will potential workers not want to work for you, but you could find that your company’s business is portrayed in the press as being not a safe place for workers, which could result in customers not wanting to do business with you.
3. How a Joint Health and Safety Committee Can help Improve Productivity
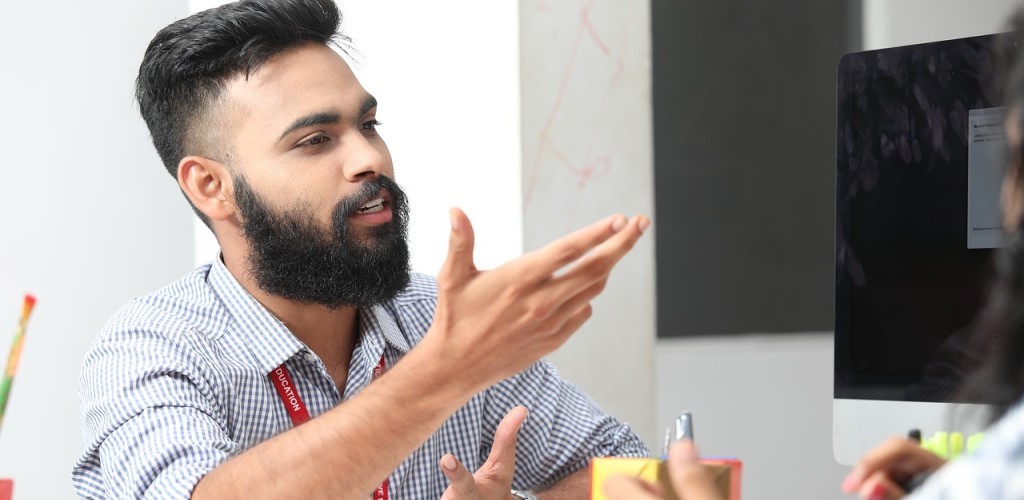
A joint health and safety committee can play a huge role in ensuring that your workplace is a safe environment
A joint health and safety committee is a group of people that represents both the workers and the employer and are mutually committed to improving the health and safety of their workplace. Together they identify potential health and safety issues in the workplace and bring those issues to the attention of the employer.
A joint health and safety committee can play a huge role in ensuring that your workplace is a safe environment. Here are some of the responsibilities that they can take on in order to help keep workers safe and thus improve your productivity:
- Inspect your workplace on a regular basis
- Identify potential and actual workplace hazards
- Get information from your employer that relates to health and safety in your workplace
- Give health and safety improvement recommendations in your workplace
- Be consulted about any health and safety-related testing in your workplace
- Have a member representing workers present at the beginning of any health and safety-related testing in your workplace
- Make themselves available to listen to and receive worker concerns, complaints, and recommendations
According to the Occupational Health and Safety Act (OHSA), at least two members of the joint health and safety committee (one representing workers and one representing persons who exercise managerial functions) need to be certified by completing Part 1 and Part 2 of mandatory Joint Health and Safety training. Once a member has been trained, they will also need to take refresher training every three (3) years in order to maintain their certification.
4. How to Get Safety Training Without Interrupting Production
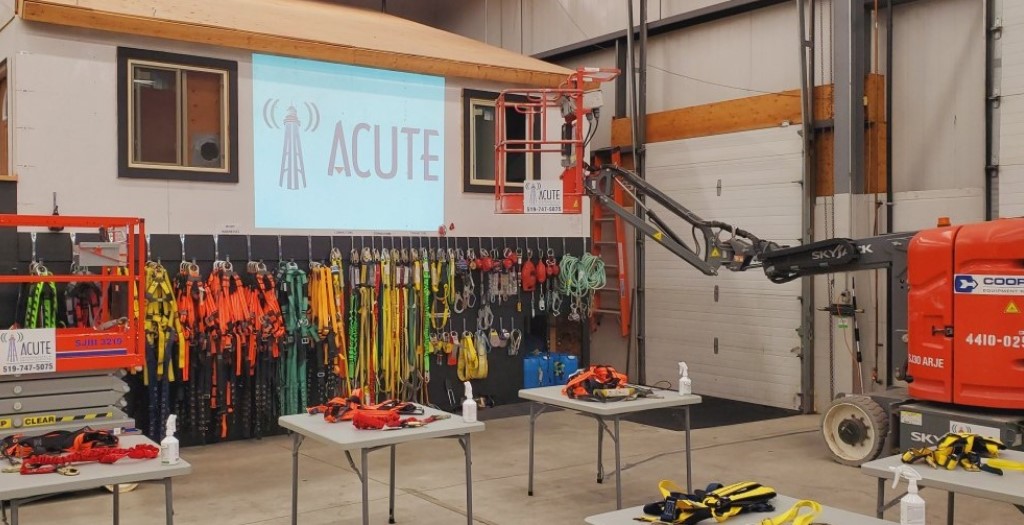
Does safety training impact production? ACUTE can do your training on the weekend
If you are concerned that getting your workers the safety training they need will interrupt production because they will need to take time off to do the training, ACUTE can help. We offer training courses on weekends too if that will help.
In addition, we can help cut down on the time that it takes for your staff to travel to our facility for training, by coming to your workplace to do the training courses you need. We want to help you in any way that we can so that your training will not impact production. We can even customize our training to best suit your particular needs.
Trust ACUTE for the Best Safety Training
ACUTE offers an incredibly wide range of health and safety courses. For a complete list of our courses, click here.
To ensure the highest level of safety in your workplace, contact the experts at ACUTE. When you take your safety training from ACUTE, you will be training with the best in the business.
ACUTE Offers:
A world-class facility with real-life simulators
Highly trained instructors with over 100 years of combined, on-site experience
Locally-based company that has a well-earned reputation for excellence and an impressive track record for success
Wide range of clients from many sectors including manufacturing, construction, health, academic, and government
Hours of Operation
Monday – Friday: 8:00am-5:00pm
Saturday – Sunday: Closed
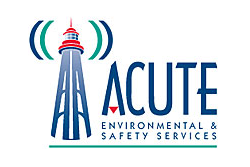
What Our Customers Are Saying…
Acute is recognized and respected as a people organization and they have been doing it right for a long time.
Acute has been a staple in supporting my companies over the years and have always delivered quality amd dependable service. Training programs are top shelf and a great facility for practical application. couldn’t recomend them more. keep up the great work folks.
We were referred to ACUTE on behalf of our employer for an n95 mask fitting – the staff here are professional, personable, and informative.
I’d come back here for any safety-related training in a heartbeat.