Emergencies don’t come with a warning—and when the pressure is on, your team must be ready to act with precision, speed, and confidence. Ontario workplaces are legally required under the Occupational Health and Safety Act (OHSA) to have emergency plans in place and ensure workers are trained to respond appropriately. The best way to test your readiness? Scenario-based emergency drills.
In this post, we break down six real-world scenarios that will help you evaluate your team’s preparedness, uncover training gaps, and strengthen your response times, keeping both your workers and your business safe.
Click on the following sections to learn more.
- Workplace Fire Drill
- Chemical Spill with Exposure Risk
- Confined Space Rescue Scenario
- Electrical Contact or Arc Flash Emergency
- Extreme Weather or Natural Disaster
- Medical Emergency on Site
- Why Scenario-Based Training Matters
- Post-Drill Debriefing: Your Improvement Tool
For more on workplace safety and emergency preparedness, contact us.
1. Workplace Fire Drill
What you see above is how NOT to conduct a workplace fire drill. Instead, try this.
Scenario: A fire breaks out near your facility’s storage area. Flames grow quickly, and smoke begins to fill adjacent hallways.
Objective: Assess evacuation efficiency, fire warden effectiveness, and alarm/communication systems.
How to Conduct the Drill:
-
Activate the fire alarm at a predetermined (but unannounced) time.
-
Ensure all staff evacuate through designated routes.
-
Time the full evacuation and verify everyone is accounted for at muster points.
-
Include a simulated “missing person” to test the response system.
Watch for Gaps:
-
Delayed evacuation or bottlenecks
-
Uncertainty about muster point locations
-
Failure to check high-risk areas (restrooms, storage rooms)
Improve With:
-
Clearly marked exits and routes
-
Appointing and training fire wardens
-
Evacuation maps at strategic locations
2. Chemical Spill with Exposure Risk
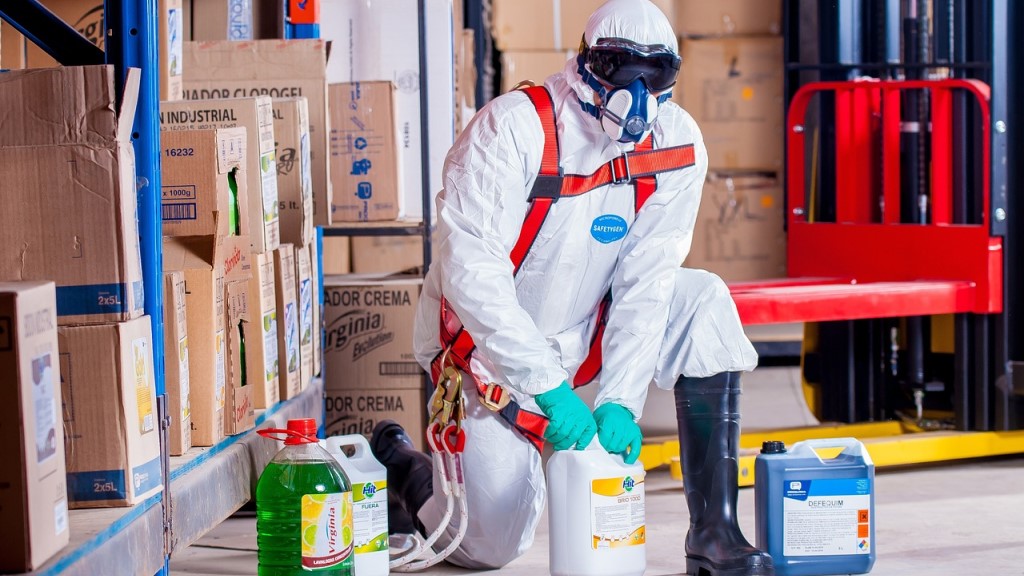
Scenario: A worker drops a container of corrosive chemical, contaminating the floor and splashing on PPE. Nearby staff must respond.
Objective: Evaluate spill containment, decontamination, and medical response protocols.
How to Conduct the Drill:
-
Simulate a spill using water and colored dye or safe training liquid.
-
Time how quickly the team identifies the spill and initiates containment.
-
Observe how the affected “worker” is moved to the eyewash station and if PPE is removed correctly.
Watch for Gaps:
-
Lack of access to spill kits or delayed use
-
Improper PPE removal techniques
-
Eyewash stations not functioning, or unfamiliarity with the location
Improve With:
-
Regular hazardous material handling refreshers
-
Spill response kits are checked monthly
-
Review of Safety Data Sheets (SDS) for each chemical on-site
3. Confined Space Rescue Scenario
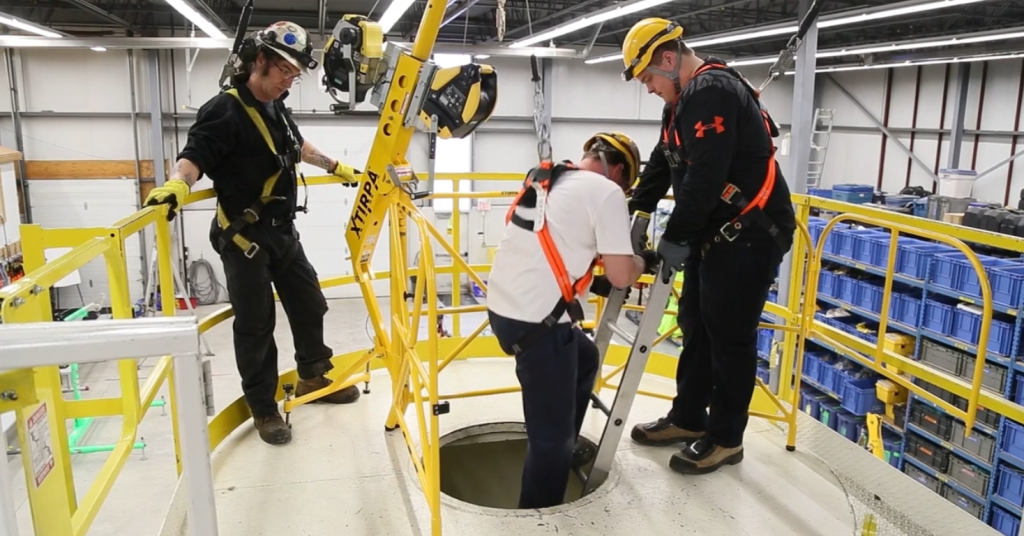
Scenario: A worker inside a confined space becomes unresponsive. Monitors detect a drop in oxygen levels. Rescue must be initiated.
Objective: Test confined space entry permits, retrieval systems, and team communication.
How to Conduct the Drill:
-
Choose a space and simulate entry with safety dummies.
-
Assign roles: entrant, attendant, rescue personnel.
-
Simulate oxygen level alarm and unresponsive worker; trigger rescue protocol.
Watch for Gaps:
-
Entry without proper gas detection or permits
-
Misuse of retrieval systems (tripod/winch)
-
Delayed communication between the entrant and the attendant
Improve With:
-
Annual confined space certification
-
Practical training with retrieval systems
-
Emergency drills every 6–12 months with documentation
4. Electrical Contact or Arc Flash Emergency
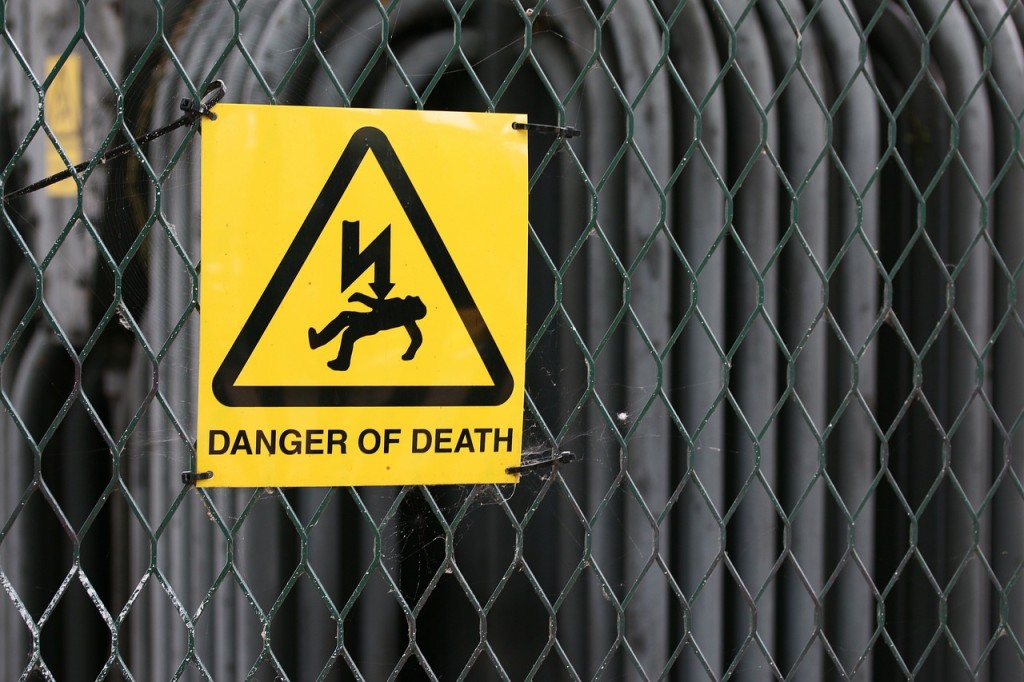
Scenario: While working on live equipment, a worker is shocked and collapses. Power needs to be cut, and first aid initiated immediately.
Objective: Test Lockout/Tagout (LOTO) procedures, CPR/AED response, and internal communication.
How to Conduct the Drill:
-
Simulate an electrical incident in a safe environment using a manikin.
-
Observe how quickly the area is isolated and if responders begin CPR or use the AED.
-
Time the entire emergency response and simulate a 911 call.
Watch for Gaps:
-
Delayed shutdown of power
-
Inability to locate or use an AED
-
Untrained responders hesitate to act
Improve With:
-
CPR and AED certification for all supervisors
-
Visible signage and training for LOTO
-
Periodic emergency walkthroughs for electrical panels
5. Extreme Weather or Natural Disaster
Scenario: Severe weather (e.g., tornado or flash flood) is imminent, and the facility must shelter in place or evacuate.
Objective: Evaluate shelter-in-place procedures and communication effectiveness.
How to Conduct the Drill:
-
Use weather alerts or simulate one internally.
-
Practice moving to designated safe zones (interior rooms, away from windows).
-
Simulate a loss of power and test alternative communication methods (radios, intercoms).
Watch for Gaps:
-
Confusion about safe zones
-
Missing or expired emergency supplies
-
Poor communication between departments
Improve With:
-
Annual emergency plan updates based on regional risks
-
Stocking and checking emergency kits
-
Weather-specific signage in key areas
6. Medical Emergency on Site
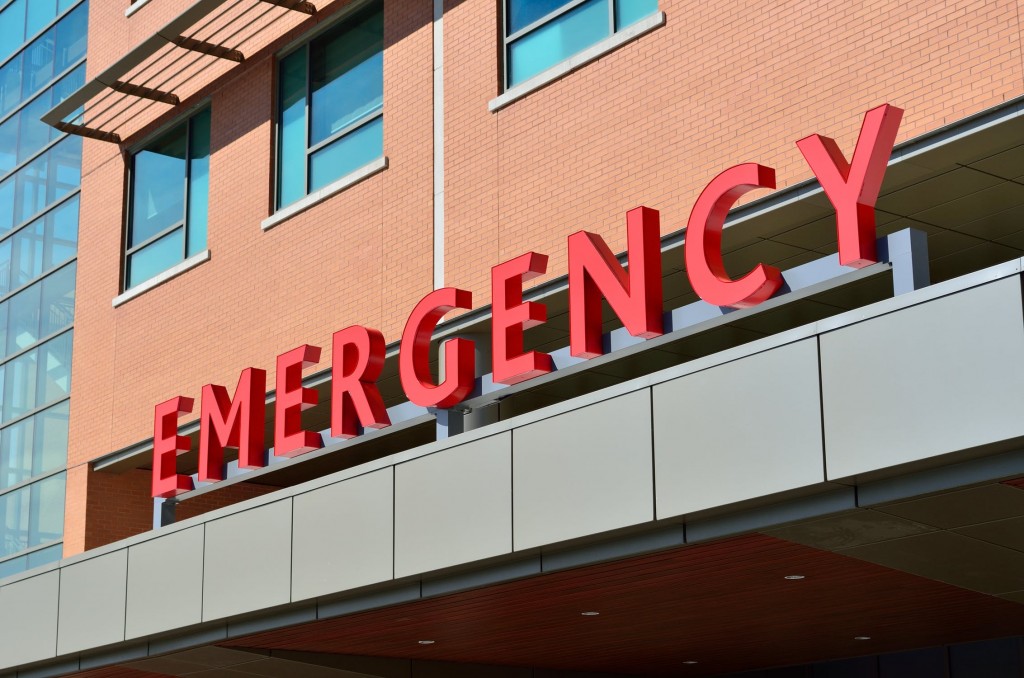
Scenario: A worker collapses from a cardiac event. Quick CPR and AED usage are required while waiting for paramedics.
Objective: Assess first aid knowledge, AED accessibility, and incident reporting.
How to Conduct the Drill:
-
Use a manikin to simulate an unconscious worker.
-
Have designated responders perform CPR and AED use.
-
Document the time to call emergency services and inform managers.
Watch for Gaps:
-
AEDs that are hard to find or access
-
Bystanders do not know what to do
-
Incomplete documentation after the incident
Improve With:
-
Marking AED locations clearly
-
First aid/CPR recertification every two years
-
Post-emergency protocols embedded in safety manuals
7. Why Scenario-Based Training Matters
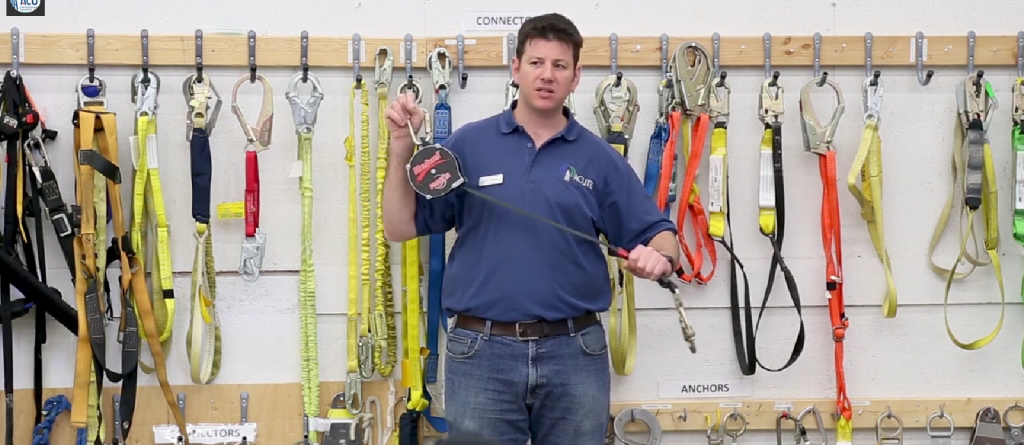
Workplace emergencies aren’t just theoretical—they’re a matter of when, not if. Fires, chemical exposures, medical incidents, and weather-related disasters all pose real threats to employee safety and business continuity. Despite having written emergency plans, many organizations fail to ensure their teams are truly prepared to respond under pressure.
This is where scenario-based training comes in. Rather than relying solely on policies and checklists, simulated drills allow your team to experience realistic, time-sensitive situations in a controlled environment. This type of hands-on practice is crucial for building competence and confidence across all departments.
Here’s how scenario-based training makes a meaningful difference:
Builds Real-Time Decision-Making Under Pressure
In an actual emergency, panic and uncertainty can cloud judgment. Drills help employees practice staying calm, prioritizing tasks, and reacting appropriately—even when alarms are blaring or a teammate is down. By simulating stress, teams learn to:
-
React without freezing
-
Rely on protocols instinctively
-
Adapt to unfolding events with confidence
Example: In a simulated confined space emergency, an attendant learns how to maintain communication and initiate non-entry rescue rather than attempting a dangerous entry.
Helps Identify Blind Spots and Procedural Flaws
No emergency plan is perfect on paper. Drills reveal gaps that may otherwise go unnoticed, such as:
-
Emergency exits blocked by storage
-
Missing spill kits or expired PPE
-
Confusion over who’s in charge during a response
Example: A simulated fire drill might uncover that the alarm system isn’t audible in the warehouse area, or that workers in one department are unaware of muster point locations.
Reinforces Roles and Chain-of-Command Responsibilities
During a real emergency, clarity around roles is critical. Drills reinforce the chain of command and ensure:
-
Supervisors know their responsibilities
-
Fire wardens or first aid responders act quickly
-
Team members don’t duplicate efforts or create confusion
Every team member should understand: What is my role? Who do I report to? What action do I take first?
Example: In a medical emergency drill, the difference between calling 911, retrieving the AED, and performing CPR must be clear and rehearsed.
Satisfies OHSA and Industry-Specific Compliance Requirements
In Ontario, the Occupational Health and Safety Act (OHSA) requires employers to take every reasonable precaution to protect workers. Scenario-based training supports compliance by:
-
Demonstrating due diligence in emergency preparedness
-
Meeting requirements in high-risk industries (e.g., confined space entry, hazardous materials handling)
-
Creating documented records of training efforts
Workplaces may also need to align with specific standards such as:
-
CSA Z1006 (management of confined spaces)
-
WHMIS 2015 training for hazardous materials
-
Emergency preparedness under ISO 45001
Failing to train effectively can result in legal liability, fines, or worse—preventable injuries and fatalities.
Fosters a Culture of Safety and Empowerment
Ultimately, scenario-based training does more than check a compliance box. It promotes a proactive safety culture where employees:
-
Feel empowered to speak up during emergencies
-
Trust that their coworkers are trained and competent
-
Are more engaged in daily safety practices
This culture extends beyond emergency situations—it boosts morale, improves retention, and helps attract workers who value safety.
Example: A company that regularly trains for high-risk scenarios is more likely to prevent everyday hazards because employees are constantly thinking one step ahead.
8. Post-Drill Debriefing: Your Improvement Tool
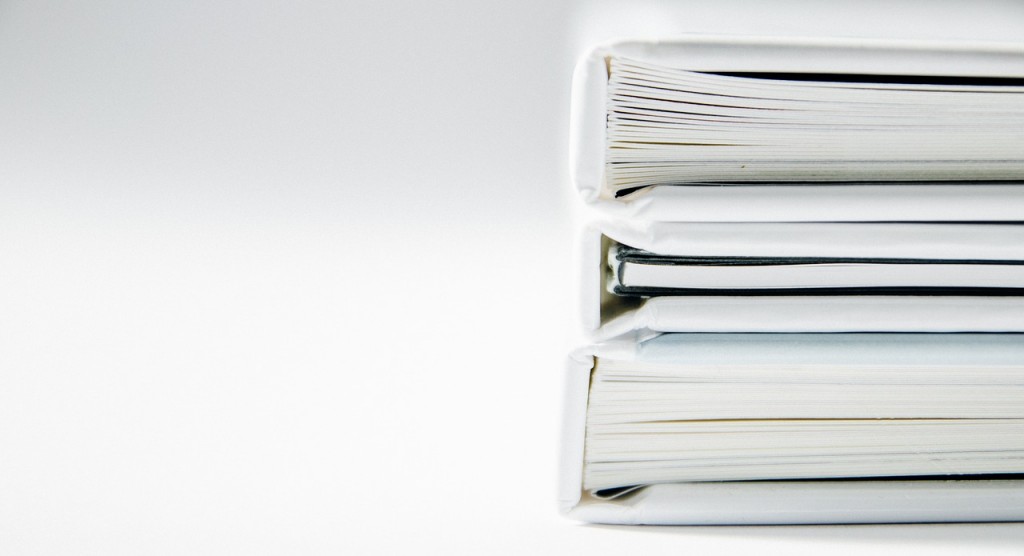
Running an emergency drill is a key step toward preparedness—but it’s the debrief that turns a simulation into lasting improvement. A structured review allows your team to identify what worked, what didn’t, and how your Emergency Response Plan (ERP) can be improved.
Here’s how to conduct an effective post-drill debrief and why it’s essential for workplace safety and compliance:
Conduct a Team Debrief While the Drill Is Fresh
Immediately after the drill, bring together all participants and observers. This includes frontline workers, supervisors, safety coordinators, and designated emergency response roles. Encourage open, honest feedback to gain a full picture of how the drill unfolded from different perspectives.
Ask questions like:
-
What went well?
-
Where did challenges arise?
-
Did everyone know their role?
-
Was there any confusion or hesitation?
Identify Strengths and Areas for Improvement
Analyze the drill results to determine where protocols were followed correctly and where breakdowns occurred. This could include:
-
Delays in evacuation or emergency communication
-
Unfamiliarity with equipment or procedures
-
Confusion over leadership roles
-
Missed steps in reporting or decontamination
The goal isn’t to assign blame but to find opportunities to improve.
Collect Input from Both Participants and Observers
Those involved in the drill provide valuable insights into how procedures felt in real time. Observers can highlight gaps that participants may not have noticed, such as:
-
Missed steps in PPE use
-
Delayed activation of emergency systems
-
Bottlenecks during evacuation
Use structured observation forms or checklists to standardize your review.
Update Your Emergency Response Plan (ERP)
Once you’ve identified gaps or weaknesses, reflect those changes in your ERP. Common updates may include:
-
Role reassignment or clarification
-
Revised evacuation routes or muster points
-
New signage or communication tools
-
Additional training for high-risk tasks
Ensure updated procedures are communicated clearly and incorporated into future training.
Keep Written Records for Compliance and Improvement
Documentation is essential. Maintain detailed records for each drill, including:
-
Date, time, and location
-
Scenario details
-
Names and roles of participants
-
Key outcomes and improvement actions
These records help demonstrate compliance with Ontario’s Occupational Health and Safety Act (OHSA) and provide a benchmark for progress over time.
Every drill should be treated as a learning opportunity. A strong debriefing process ensures your team becomes more prepared with every exercise, and your organization stays aligned with legal and safety requirements.
Is Your Team Ready to Respond? Put Them to the Test.
Emergency preparedness isn’t just about having policies on paper—it’s about making sure your team can respond under pressure. These 6 real-world scenarios are designed to help you identify gaps, strengthen response times, and meet Ontario’s workplace safety standards.
Not sure where to start? ACUTE can help.
We provide comprehensive health and safety training, on-site safety services, and consulting designed to prepare your team for the unexpected.
Why Choose ACUTE?
-
Extensive Experience: With over 100 years of combined on-site experience, our team delivers more than just theory—we bring real-world insight into every training session.
-
First-Rate Trainers: Our instructors are experienced professionals who make safety training hands-on, engaging, and practical.
-
Tailored Training Solutions: Every workplace is different. We customize our training to align with your specific industry, policies, and emergency procedures.
-
Convenient Location: Located in Waterloo, we proudly serve all of Ontario and have supported clients coast to coast.
-
World-Class Facility: Our advanced training centre is among the best in Canada and well worth the visit for organizations serious about safety
Test Your Team. Strengthen Your Response. Stay Compliant.
Whether you need help designing custom emergency drills or want certified, high-impact training to prepare your team, we’re ready to support you.
Contact ACUTE today to schedule a consultation or book training for your team.
Let us help you turn emergency planning into emergency readiness.
What Our Customers Are Saying…
Acute is recognized and respected as a people organization and they have been doing it right for a long time.
Acute has been a staple in supporting my companies over the years and have always delivered quality amd dependable service. Training programs are top shelf and a great facility for practical application. couldn’t recomend them more. keep up the great work folks.
We were referred to ACUTE on behalf of our employer for an n95 mask fitting – the staff here are professional, personable, and informative.
I’d come back here for any safety-related training in a heartbeat.