If you are a business owner, supervisor, manager, or even an employee, and you work with controlled products you need to be familiar with safety data sheets (SDSs), formerly known as material safety data sheets (MSDSs). Understanding how to read the information on these sheets will promote safety in the workplace and keep everyone safe.
In this article, we will go over what a safety data sheet is, how to read one, and all workplace responsibilities.
Click on each corresponding link to jump ahead to that section:
If you have questions regarding health and safety in the workplace or safety training, contact the professionals at ACUTE Environmental today! We have over 100 years of combined experience and we offer health and safety training, rescue services, and consulting services.
Safety Data Sheet (SDS): Everything You Need to Know
1. What Is an SDS?
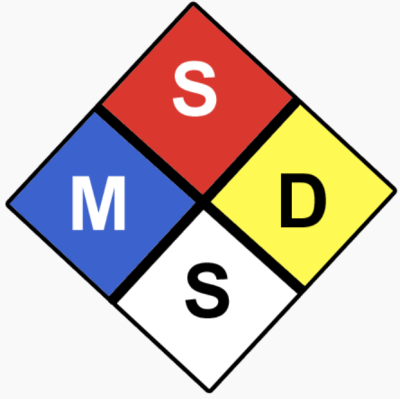
Make sure you fully understand what an SDS is (formerly known as an MSDS).
According to the Canadian Centre for Occupational Health and Safety (CCOHS), a safety data sheet (SDS), formerly referred to as a material safety data sheet (MSDS), “is a document that contains information on the potential hazards (health, fire, reactivity and environmental) and how to work safely with the chemical product.”
An SDS also encompasses guidance on the material’s appropriate usage, storage, handling, and emergency procedures in relation to its hazards.
These sheets are generated by the supplier or manufacturer of the material and aim to inform users about the:
- Product’s dangers
- Safe handling practices
- Consequences of non-compliance with guidelines
- Actions to take in case of accidents
- Methods to identify overexposure symptoms
- How to respond to such incidents
For more information on SDSs check out the following video:
Overall, it is important that you understand how to read an SDS so you can effectively comply. If you are seeking the most up-to-date materials safety information, check with your supervisor/materials provider. For training on how to properly read an SDS and handle, use, and store hazardous materials in the workplace, click here.
2. How to Read an SDS
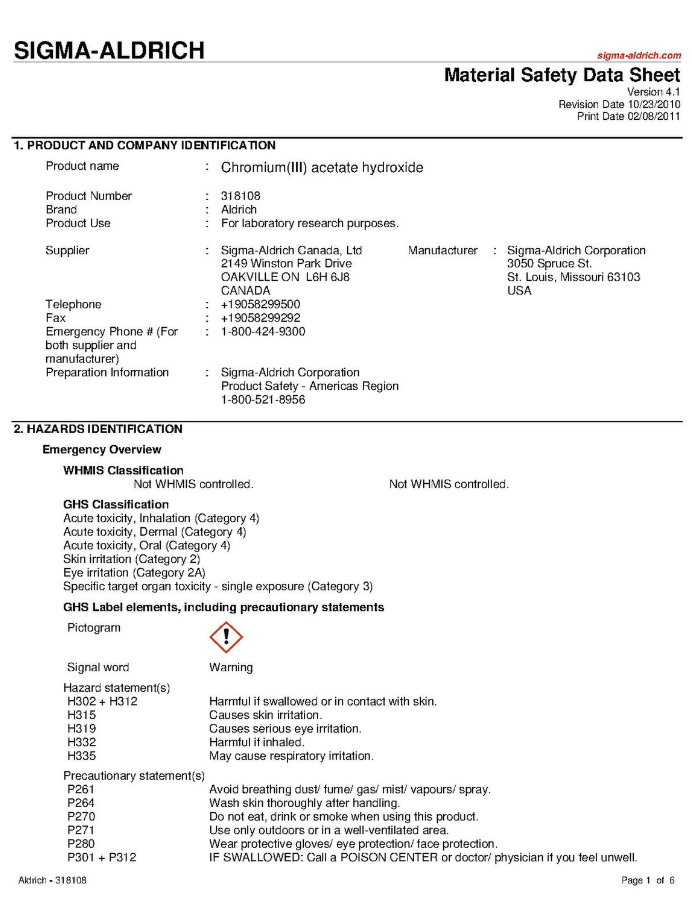
Here is an example of an SDS.
It is no secret that SDSs are difficult to read. This is because they were originally designed for hygienists and safety professionals. However, those that require SDSs have expanded and now include:
- Employers
- Supervisors
- Workers (doctors and nurses)
Given this, it is essential that SDSs are designed in a way that is easy to read and understandable.
It is also important to note that you should be reading the SDS BEFORE you use the product. Educate yourself on the potential risks prior to use.
To understand how to read an SDS, you must be made aware of its 9 categories of information. These include:
- Product Information: This section contains basic details about the product, such as its name, intended use, manufacturer or supplier information, emergency contact numbers, and the date the SDS was prepared or last updated (should not be more than 3 years old). It helps you identify the specific product you are dealing with and provides essential contact information in case of emergencies.
- Hazardous Ingredients: In this section, the SDS lists all hazardous ingredients present in the product, along with their Chemical Abstracts Service (CAS) numbers and concentrations. Hazardous ingredients are substances that could pose health, safety, or environmental risks.
- Physical Data: Here, you’ll find information on the physical and chemical characteristics of the product. It includes details such as appearance, odour, colour, boiling point, melting point, vapour pressure, density, solubility, and pH. Understanding these properties helps assess the potential risks and appropriate handling methods.
- Fire or Explosion Hazard Data: This section provides guidance on the product’s flammability and potential risks of fire or explosions. It includes flashpoint, autoignition temperature, flammability limits, and firefighting measures, helping responders understand how to tackle fire emergencies involving the substance.
- Reactivity Data: Reactivity data highlights the product’s chemical stability and potential reactivity with other substances. It includes information on conditions to avoid (e.g., heat, water, specific chemicals) to prevent hazardous reactions.
- Toxicological Properties: The toxicological properties section outlines the potential health effects of the product and its hazardous ingredients. It covers acute and chronic toxicity data, exposure routes (e.g., inhalation, ingestion, skin contract), and symptoms of exposure.
- Preventative Measures: Here, you’ll find information on safety precautions and control measures to minimize risks when handling the product. This may include engineering controls (e.g., ventilation), personal protective equipment (PPE) recommendations, and safe storage practices.
- First Aid Measures: This section provides instructions on what immediate actions to take in case of exposure to the product. It covers first aid procedures for various types of exposures, such as inhalation, skin contact, eye contact, and ingestion.
- Preparation Information: The preparation information section includes details about the preparation or revision of the SDS. It may contain the name and contact information of the company of experts responsible for compiling the data.
It is important to note the layout and content of an SDS may vary depending on regional regulations and standards, but the essential information remains consistent to ensure the safe handling and use of chemical products. Always refer to the SDS provided by the manufacturer or supplier when working with hazardous materials.
3. Workplace Responsibilities
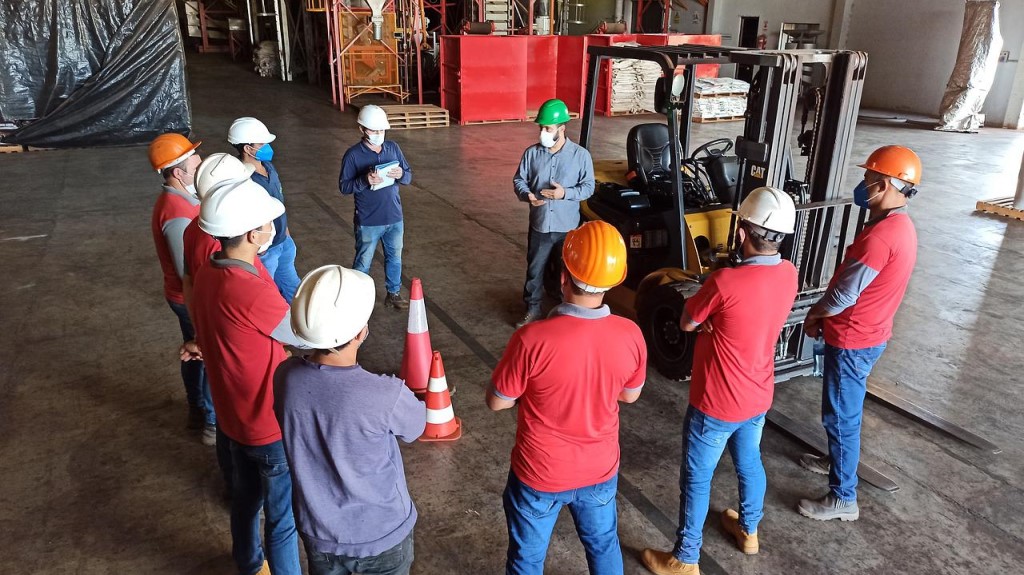
As an employer, make sure each product has an SDS no older than 3 years.
At ACUTE, we are constantly discussing the importance of workplace safety and producing a positive work culture. As an employer, one way to do this is to ensure you meet all SDS requirements.
If you are an employer, you must make sure that all controlled products have an SDS that is up to date. This means that the SDS can not be more than three years old. If it is older than three years, contact the manufacturer or supplier and ask for an updated version.
Also, each SDS must be made readily available to all workers and health and safety representatives who are exposed to the product. These SDSs can be computerized as long as all employees have a computer they can use and know how to access the information. If you do decide to computerize these sheets, still make sure you have hard copies available upon request.
If your workplace produces these controlled products, it is the employer’s responsibility to prepare an SDS for these products.
Lastly, if you are an employer, health and safety representative, a member of the health and safety committee, or even an employee, ensure everyone is properly trained on SDS. Sign up for WHMIS training today and learn how to identify potential risks, safely handle controlled products, and navigate an SDS.
Work With ACUTE Environmental
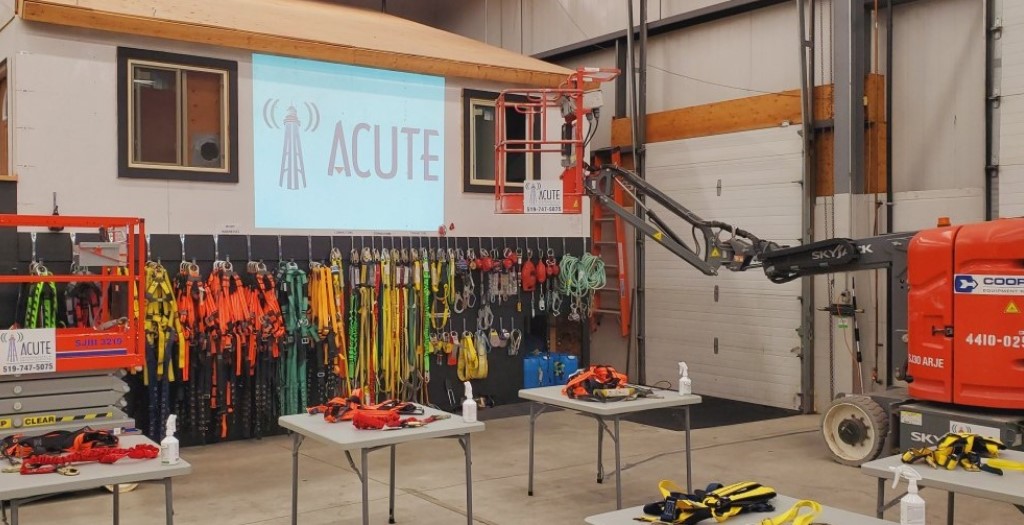
ACUTE can help you better understand the importance of SDS's.
If you are in charge of supervising health and safety in the workplace and are looking for high-quality online safety training or in-person safety training, book a course with ACUTE. Also, if you have any questions regarding SDSs, contact us.
Here are some of the benefits of working with ACUTE:
- Open Door Instructor-Student Partnership – ACUTE’s training services emphasize client participation, staff foster relationships with clients and serve as a touchstone for advice anytime moving forward.
- Serving Your Team and Industry – With a vast array of clients in manufacturing, construction, health, academic, and government sectors, ACUTE brings the best safety practices from across the spectrum to your workplace.
- 100 Years Combined Experience – ACUTE provides comprehensive health and safety training, on-site safety services, and consulting services. With over 100 years of combined experience, our company staff offers more than theoretical or abstract ideas. ACUTE offers solutions!
- Track Record of Success – ACUTE is rated 4.9/5 stars on Google reviews, demonstrating our commitment to our clients, our quality, and our passion for training.
Take a look at our course calendar, and find a date that works for you! We offer courses such as:
For a complete list of our training courses, click here.
Hours of Operation and Contact Information:
Monday-Friday: 8:00 AM – 5:00 PM
Saturday-Sunday: Closed
Phone: (519) 747-5075
Fax: (519) 747-4608
Email: info@acuteservices.com
What Our Customers Are Saying…
We were referred to ACUTE on behalf of our employer for an n95 mask fitting – the staff here are professional, personable, and informative.
I’d come back here for any safety-related training in a heartbeat.
Acute has been a staple in supporting my companies over the years and have always delivered quality and dependable service. Training programs are top shelf and a great facility for practical application. couldn’t recommend them more. keep up the great work folks.
Acute is recognized and respected as a people organization and they have been doing it right for a long time.