By 2030, advancements in artificial intelligence (AI), automation, and remote work will significantly reshape workplace safety and specifically how businesses protect their employees.
From innovative personal protective equipment (PPE) to AI-powered compliance monitoring, technological progress will likely prompt updates to occupational safety laws. For businesses, staying proactive will be essential to remaining compliant and safeguarding their workforce.
In this article, we’ll explore how workplace safety could change by 2030, the innovations driving these shifts, and how companies can prepare for a safer and more compliant future.
Click on the links below to learn more.
- The Role of AI in Workplace Safety Compliance
- Automation and the Reduction of Workplace Hazards
- Remote Work and Evolving Workplace Safety Standards
- Innovations in Personal Protective Equipment
- How Businesses Can Prepare for the Future of Workplace Safety
If you’re ready to improve safety training for your workplace, contact us for expert advice and resources tailored to your organization’s needs.
1. The Role of AI in Workplace Safety Compliance
By 2030, AI-powered systems will monitor worksites in real time, identifying hazards and ensuring compliance with regulations. Cameras equipped with computer vision can detect unsafe behavior, while predictive analytics can forecast potential risks based on historical data.
Additionally, AI can analyze employee behavior to predict unsafe patterns and suggest corrective actions before incidents occur. Natural language processing (NLP) systems may monitor incident reports to detect trends and recommend preventive measures. Some companies are even adopting digital twins—virtual simulations of worksites—to test safety protocols and optimize layouts for hazard reduction.
Key Developments to Expect:
- Automated compliance auditing through AI-driven reporting tools
- Real-time hazard detection and alerts
- AI-assisted training programs to reinforce safety practices
- Predictive analytics for risk assessment
- Voice-activated reporting systems for on-the-spot incident reporting
Businesses should invest in AI-powered safety management platforms to maintain compliance and reduce the risk of violations. Collaborating with AI solution providers and integrating these tools into their operations will ensure a proactive approach to safety.
2. Automation and the Reduction of Workplace Hazards
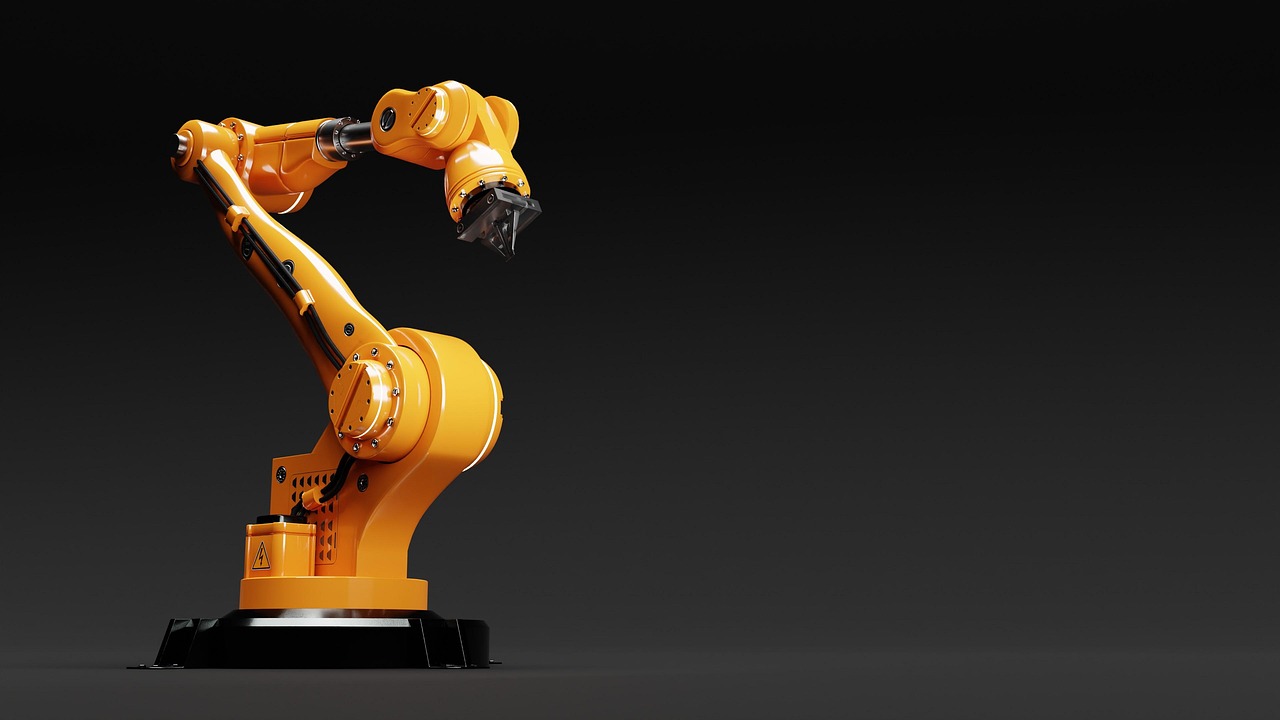
Automation will continue to replace repetitive, hazardous tasks, making work sites safer. Robotics and automated machinery will handle dangerous operations in manufacturing, construction, and logistics. By reducing human exposure to risky environments, automation will significantly reduce workplace injuries and fatalities.
In industries like warehousing and logistics, autonomous vehicles and drones can transport materials, inspect hazardous environments, and perform maintenance in dangerous areas. Automated machinery equipped with AI-driven sensors will monitor conditions, predicting equipment failures before they occur, preventing accidents.
Potential Innovations:
- Collaborative robots (cobots) that work alongside employees
- Autonomous vehicles and drones for hazardous site monitoring
- AI-powered sensors to detect machine malfunctions before accidents occur
- Robotic exoskeletons to reduce strain on workers performing physical tasks
- Predictive maintenance software that minimizes downtime and safety risks
Regulators may introduce new guidelines around the safe use of automation. Companies should anticipate stricter oversight and ensure their automated systems meet updated standards. Implementing regular audits and inspections will further minimize risks.
3. Remote Work and Evolving Workplace Safety Standards
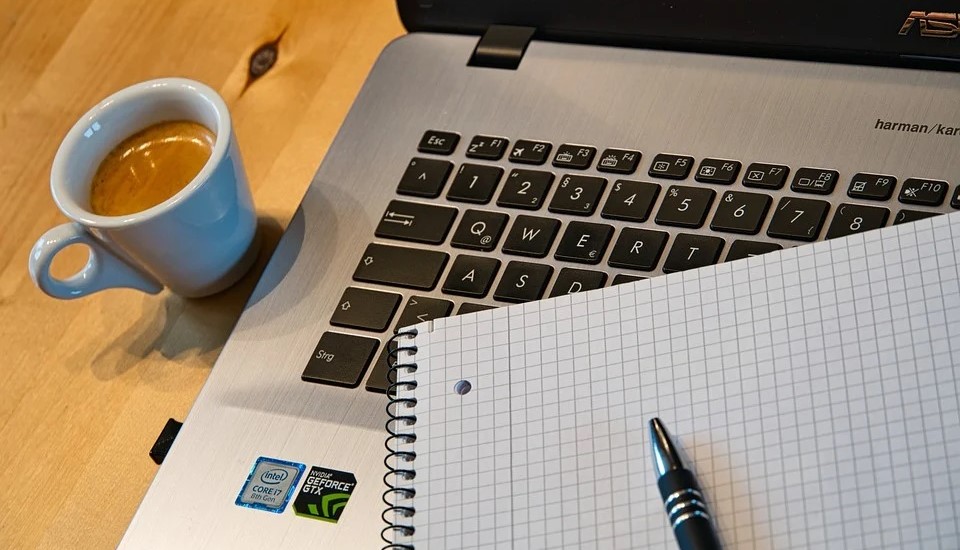
The rise of remote and hybrid work has introduced new challenges for occupational safety. By 2030, expect laws to address ergonomic issues, mental health, and digital security. While remote employees may not face traditional workplace hazards, long hours at poorly designed home workstations can lead to musculoskeletal disorders.
Mental health will also become a more prominent aspect of workplace safety. Employers will likely be required to provide mental health resources, counseling, and regular wellness check-ins. Additionally, cybersecurity regulations may expand to ensure remote employees follow proper data protection protocols.
Future Changes May Include:
- Employer-provided ergonomic assessments for home offices
- Enhanced mental health support programs
- Cybersecurity protocols to protect remote workers’ data
- Virtual safety training and compliance certifications
- AI-powered mental health assessment tools
- Wearable technology to monitor posture and activity levels
Companies should establish remote work safety policies and provide employees with resources to maintain a healthy and secure workspace. Ergonomic assessments, standing desks, and proper screen positioning are simple yet effective ways to minimize remote work-related injuries.
4. Innovations in Personal Protective Equipment (PPE)
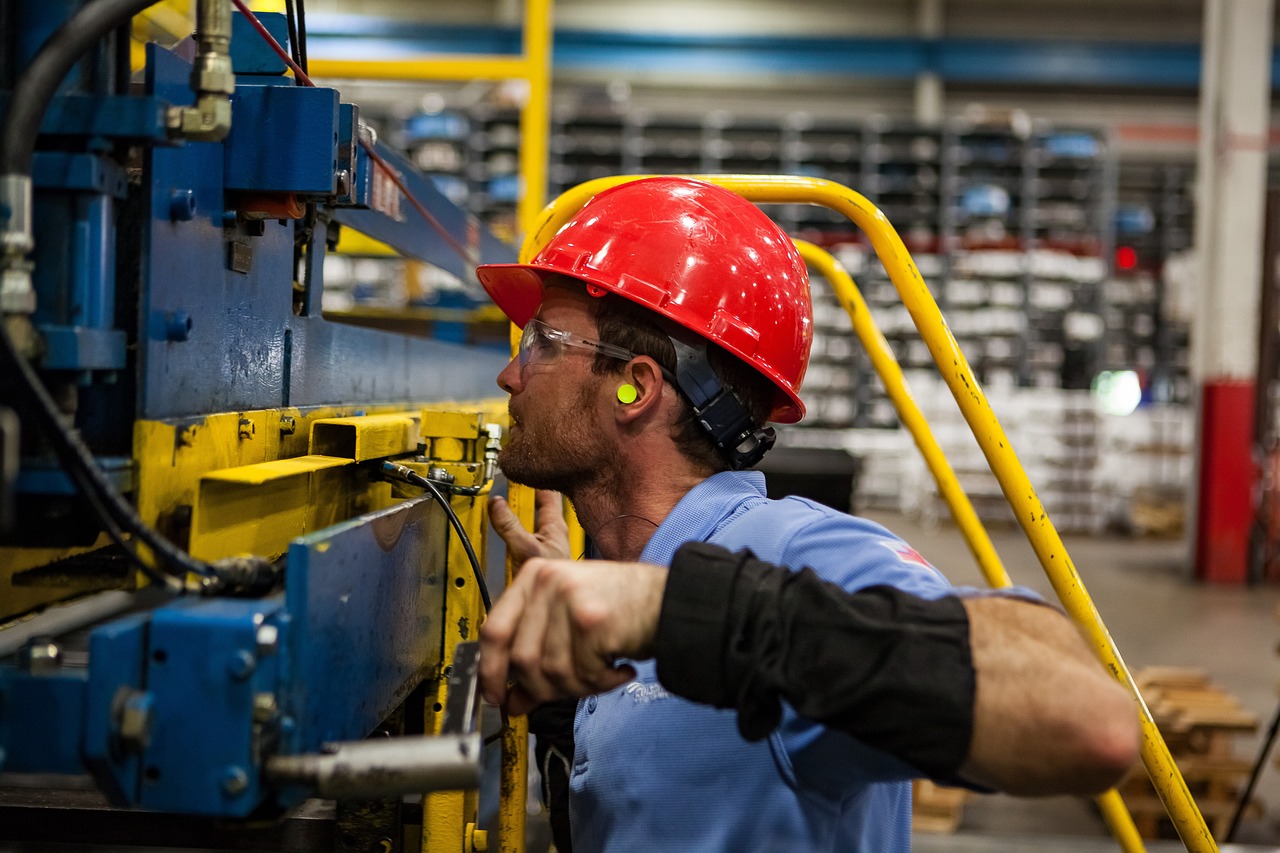
Next-generation PPE will integrate cutting-edge technology to enhance safety. From smart helmets that detect impacts to augmented reality (AR) safety glasses providing real-time instructions, the future of PPE is promising.
Smart PPE will feature biometric sensors to monitor workers’ vitals, ensuring they are not overexerted or exposed to harmful conditions. Real-time data will allow supervisors to respond quickly to emergencies. Some wearable devices may also detect toxic gases or temperature extremes.
Examples of Upcoming Innovations:
- Smart sensors embedded in clothing to monitor vital signs
- Exoskeletons to reduce strain and prevent injuries
- AR wearables for hands-free communication and hazard identification
- Impact-detection helmets that send alerts during accidents
- Smart gloves that provide haptic feedback for safer machinery operation
- Temperature-regulating fabrics to prevent heat stress
Businesses should remain informed about advancements in PPE and adopt solutions that offer enhanced protection. Partnering with manufacturers specializing in smart PPE can ensure workers have access to the latest safety innovations.
5. How Businesses Can Prepare for the Future of Workplace Safety
To stay compliant and protect their workforce, businesses can take proactive steps:
- Invest in AI and Automation: Evaluate AI-powered safety tools and automation to minimize workplace risks.
- Enhance Training Programs: Implement digital safety training, including VR simulations for realistic hazard scenarios.
- Review Remote Work Policies: Regularly assess and update remote work guidelines to align with evolving regulations.
- Stay Updated on Regulations: Partner with legal and compliance experts to track changes in occupational safety laws.
- Adopt Smart PPE: Test and integrate wearable technology to enhance worker safety.
- Develop a Safety Culture: Encourage open communication about safety concerns and provide incentives for safe behavior.
- Leverage Data for Insights: Use data analytics to identify patterns and continuously improve workplace safety protocols.
By fostering a proactive safety culture and embracing technological advancements, businesses will ensure compliance while protecting their employees.
By 2030, workplace safety regulations will reflect the increasing influence of AI, automation, and remote work. Businesses that proactively adopt new technologies and adapt to evolving standards will not only ensure compliance but also foster a safer and more resilient workforce. Staying ahead of these changes today will lead to long-term success in the years to come.
For more insights on workplace safety and compliance strategies, stay tuned to our blog or contact us for personalized solutions tailored to your industry.
Stay On Top of Workplace Safety Training With ACUTE
ACUTE Environmental & Safety Services is excited to announce its partnership with SafetyCo Partners, a leader in integrated health and safety solutions.
This investment will expand ACUTE’s Waterloo Safety Centre of Excellence, doubling our capacity to deliver confined space services and allowing us to train 10,000 more workers annually across the construction, manufacturing, and industrial sectors.
With nearly 30 years of experience, ACUTE remains committed to delivering hands-on, experience-driven safety training—now with enhanced resources and technology to help even more workers stay safe on the job.
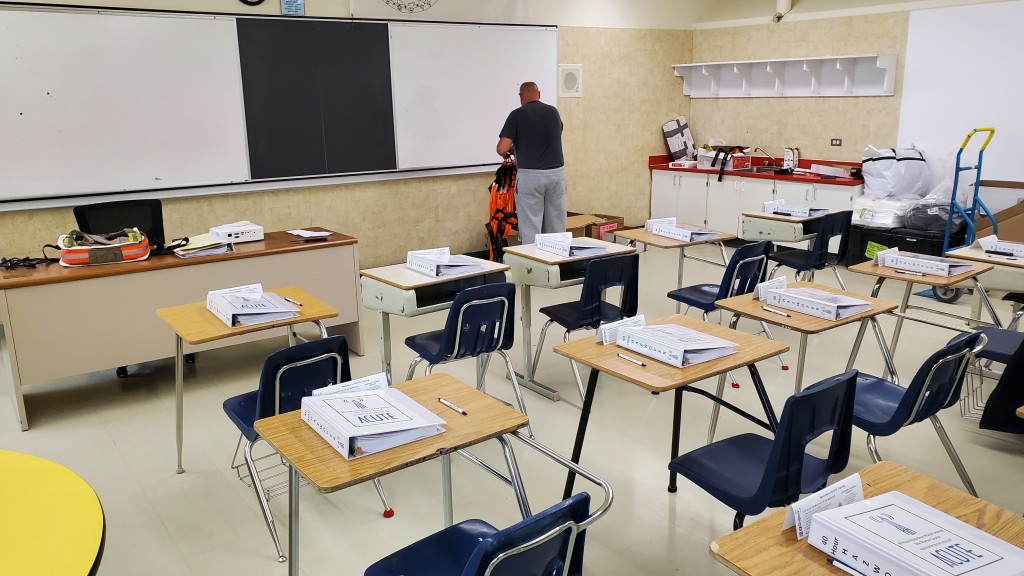