Overlooked hazards in warehouses can result in preventable injuries, operational downtime, and even legal penalties. While most Ontario warehouses meet the basic requirements outlined in the Occupational Health and Safety Act (OHSA), some risks can quietly escalate due to routine oversight or a lack of awareness. Issues like improper racking, unsafe pedestrian routes, and poor lighting may not seem urgent—until something goes wrong.
This blog post highlights some of the most commonly ignored warehouse hazards, outlines clear solutions, and explains the importance of regular assessments and training updates to maintain a safe and efficient work environment.
Click on the following sections to learn more.
For more on overlooked hazards and workplace safety, contact us.
1. Improper Racking and Storage Systems
The Hazard:
Warehouse racking systems are often taken for granted until they become unstable or collapse. Over time, racks can become damaged due to repeated forklift contact, poor pallet placement, or overloading. Without routine inspections, small issues like a missing safety pin or warped beam can lead to major failures, resulting in injuries, product damage, or worse.
The Fix:
Ensure that all racking systems are professionally installed and meet CSA (Canadian Standards Association) safety requirements. Regularly inspect racks for signs of structural wear, including dents, rust, or missing locking mechanisms. Post clearly visible weight limits on each bay and train workers to never exceed them. Create a checklist and assign someone responsible for monthly racking inspections.
Training Suggestion:
Offer annual refresher training on proper pallet loading, racking inspection basics, and forklift/rack interaction protocols. Consider including real-life incident case studies to reinforce the risks.
2. Inadequate Pedestrian Traffic Flow
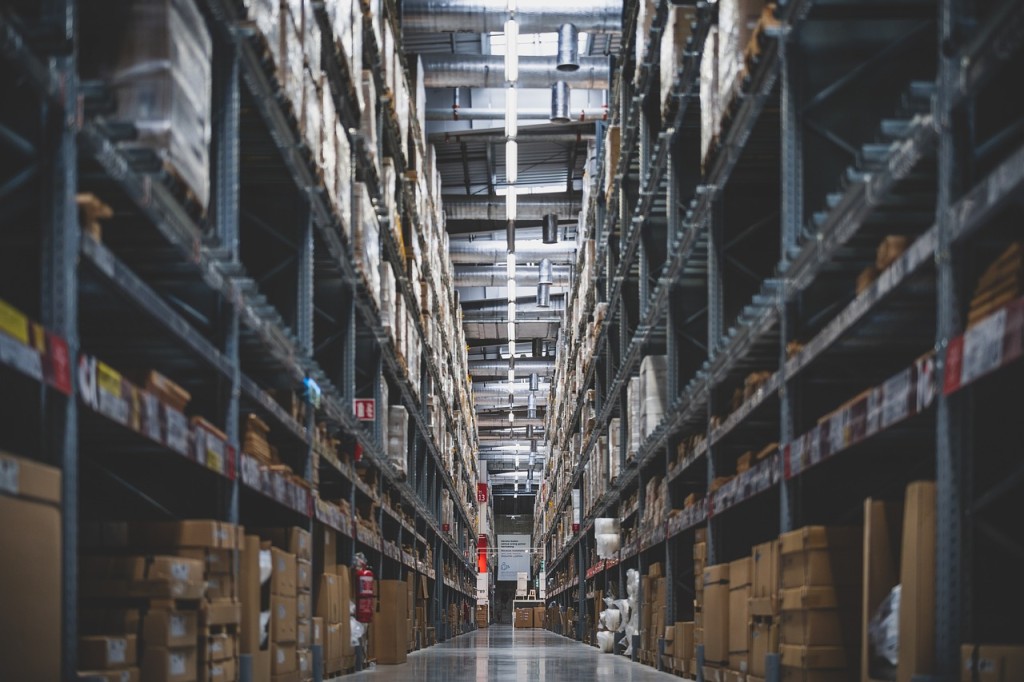
The Hazard:
In a busy warehouse, it’s easy for pedestrian safety to be compromised. When workers on foot share space with forklifts and other moving equipment without clear boundaries, the risk of accidents increases significantly. Blind corners, unmarked crossings, and high-traffic intersections are especially dangerous.
The Fix:
Create clearly defined pedestrian walkways using high-visibility floor markings or paint. Where possible, separate pedestrian and equipment traffic with physical barriers such as guardrails or bollards. Install convex mirrors at blind intersections and ensure signage is in place to alert both drivers and walkers to potential hazards.
Procedural Update:
Develop and implement a warehouse traffic management plan that outlines speed limits, one-way routes, crossing protocols, and pedestrian right-of-way rules. This plan should be reviewed and updated annually or whenever the layout changes.
Training Suggestion:
Incorporate traffic safety into onboarding programs and conduct walkthrough drills for new and seasonal staff. Regular safety talks should reinforce the shared responsibility between drivers and pedestrians.
3. Poor Lighting in Work Areas and Aisles
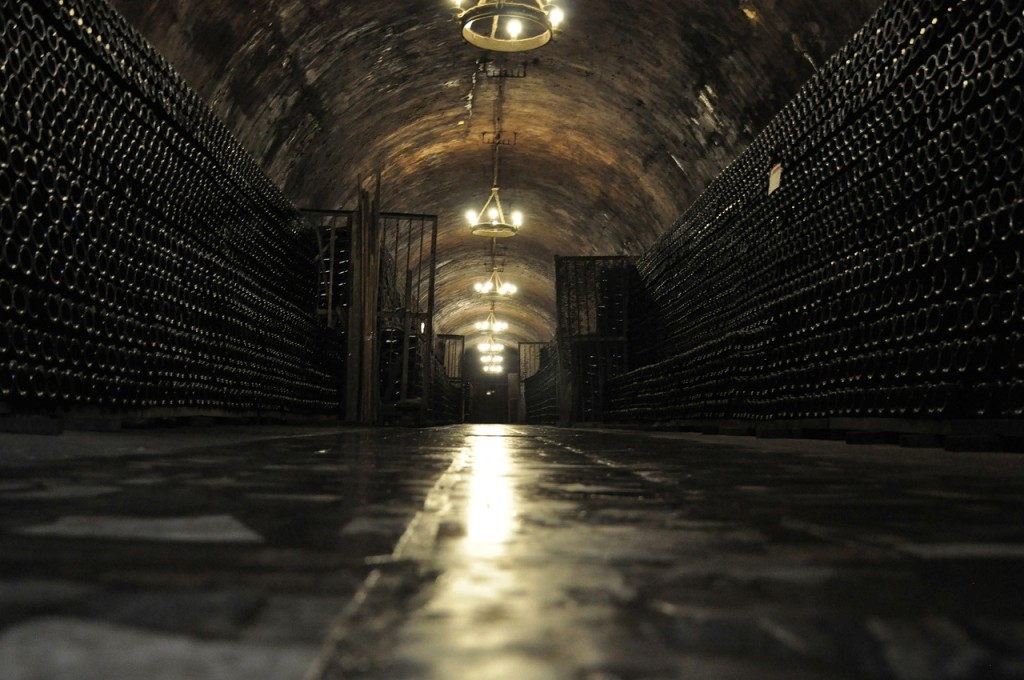
The Hazard:
Insufficient or uneven lighting in a warehouse creates conditions where workers can’t clearly see obstructions, labels, or movement. Poor visibility increases the chance of slips, trips, and collisions—especially in loading areas, between racks, or in storage mezzanines.
The Fix:
Upgrade existing lighting to high-efficiency LED fixtures that offer consistent brightness throughout the facility. Place special focus on illuminating workstations, emergency exits, and high-traffic zones. Install motion-sensor lighting in lesser-used areas to save energy without sacrificing safety.
Maintenance Practice:
Establish a monthly inspection schedule to clean dust off light covers, replace burned-out bulbs, and check for flickering lights. Ensure workers know how to report lighting issues and follow up promptly with fixes.
Training Suggestion:
Include lighting inspections as part of your regular supervisor walk-throughs. Encourage team members to document lighting concerns on digital hazard reporting forms or logbooks.
4. Blocked Emergency Exits and Equipment
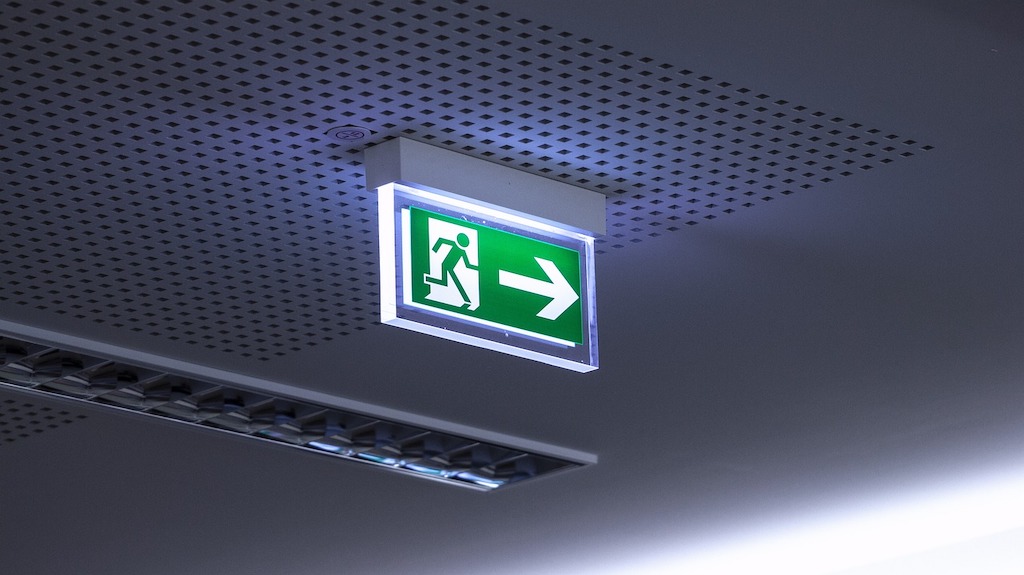
The Hazard:
In fast-paced warehouse environments, it’s not uncommon for pallets, carts, or inventory overflow to block emergency exits, fire extinguishers, and eyewash stations. During an emergency, any delay in accessing this equipment can have life-threatening consequences.
The Fix:
Designate a clear safety zone—typically at least 1 meter—around all emergency exits, fire equipment, and first aid stations. Mark these zones on the floor using bright tape or painted lines. Conduct weekly spot checks to ensure nothing is blocking these critical areas.
Procedural Update:
Add emergency access verification to your shift change protocols and daily pre-shift safety checklist. Supervisors should be held accountable for ensuring their sections remain clear.
Training Suggestion:
Incorporate equipment and exit clearance training into your annual fire safety drills and emergency preparedness sessions. Remind staff that blocking access—even temporarily—is a safety violation.
5. Lack of Routine Hazard Assessments
The Hazard:
Many warehouses conduct a one-time hazard assessment and then fail to revisit it. But operations evolve – new equipment is added, seasonal staff are hired, and layouts change. Without regular evaluations, new risks can remain unnoticed and unmitigated.
The Fix:
Conduct formal hazard assessments on a quarterly basis, led by a trained health and safety representative or Joint Health and Safety Committee member. Use a standardized checklist to ensure nothing is missed. Act promptly on any issues identified and document all corrective actions.
Ongoing Improvement:
Encourage workers to participate in a culture of safety by reporting new hazards or near-misses using a simple reporting system—paper, mobile app, or shared digital form. Create a system of follow-ups and feedback to show that their input is valued and leads to change.
Training Suggestion:
Host quarterly safety meetings where trends and assessment results are shared. Recognize departments that show proactive improvement or high participation in hazard reporting.
Don’t Let Overlooked Hazards Become Catastrophic Events
Maintaining a safe warehouse environment requires constant vigilance and a proactive mindset. The overlooked hazards mentioned in this article—like improper racking, inadequate lighting, and pedestrian traffic confusion—might seem minor, but they can snowball into major issues if not addressed.
By committing to regular inspections, improving training programs, and fostering a culture of continuous safety awareness, Ontario warehouse operators can protect both their workers and their bottom line.
Not sure where to start? ACUTE can help.
We provide comprehensive health and safety training, on-site safety services, and consulting designed to prepare your team for the unexpected.
Why Choose ACUTE?
-
Extensive Experience: With over 100 years of combined on-site experience, our team delivers more than just theory—we bring real-world insight into every training session.
-
First-Rate Trainers: Our instructors are experienced professionals who make safety training hands-on, engaging, and practical.
-
Tailored Training Solutions: Every workplace is different. We customize our training to align with your specific industry, policies, and emergency procedures.
-
Convenient Location: Located in Waterloo, we proudly serve all of Ontario and have supported clients coast to coast.
-
World-Class Facility: Our advanced training centre is among the best in Canada and well worth the visit for organizations serious about safety
Test Your Team. Strengthen Your Response. Stay Compliant.
Whether you need help designing custom emergency drills or want certified, high-impact training to prepare your team, we’re ready to support you.
Contact ACUTE today to schedule a consultation or book training for your team.
Let us help you turn emergency planning into emergency readiness.
What Our Customers Are Saying…
Great training facilities and knowledgeable staff. Highly recommended!