In the dynamic landscape of Ontario workplaces, understanding and adhering to Ontario safety laws and regulations is paramount to fostering a secure and healthy environment for both employers and employees.
The province has implemented a comprehensive set of safety laws, each addressing specific facets of occupational well-being. This article will delve into key components of the Ontario safety framework, covering pivotal legislation such as the Occupational Health and Safety Act (OHSA), the Workplace Hazardous Materials Information System (WHMIS), the importance of Personal Protective Equipment (PPE), and specific training and certification requirements for specialized scenarios.
Click on each corresponding link to jump ahead:
- Occupational Health and Safety Act (OHSA)
- Workplace Hazardous Materials Information System (WHMIS)
- Personal Protective Equipment (PPE)
- Specific Requirements
If you have any questions or concerns regarding Ontario safety laws and regulations, contact ACUTE Environmental directly.
Ontario Safety Laws
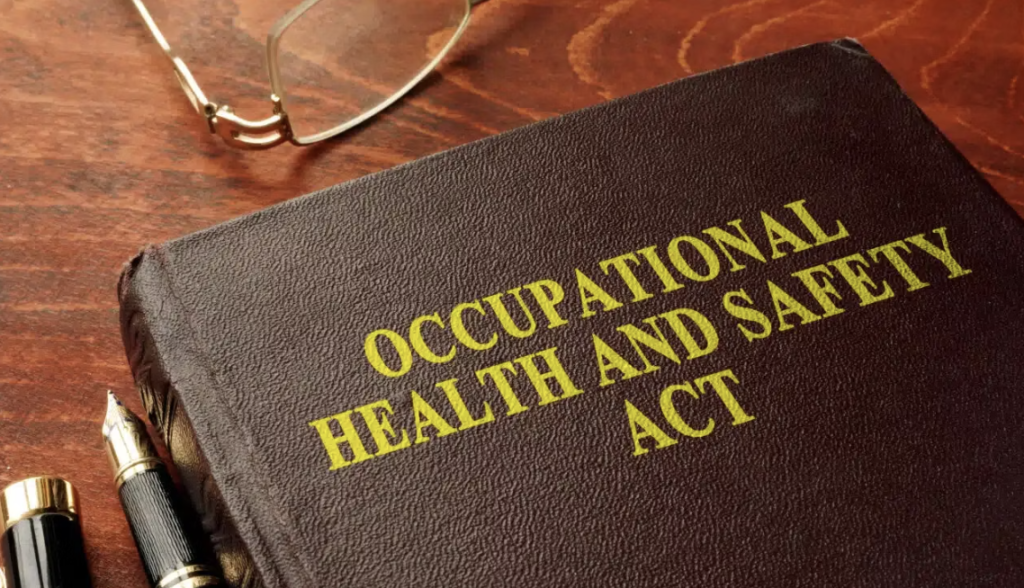
The OHSA governs Ontario safety laws.
1. Occupational Health and Safety Act (OHSA)
The OHSA is the primary legislation governing workplace health and safety in Ontario. It outlines the rights and responsibilities of employers, supervisors, and workers to ensure a safe working environment. Here are some key aspects and details about the OHSA:
A) Purpose and Scope
The primary purpose of the OHSA is to protect workers from health and safety hazards in the workplace.
The OHSA applies to almost all workplaces in the province of Ontario, including industrial, construction, healthcare, and office environments.
B) Rights and Responsibilities
Visit the OHSA website to learn more about Ontario safety laws.
The OHSA outlines the rights and responsibilities of three main parties:
- Employers
- Supervisors
- Workers
Employers are responsible for:
- Providing a safe and healthy work environment
- Ensuring compliance with the OHSA
- Providing information and training to workers
Supervisors are required to ensure that workers work safely and use the provided protective equipment.
Workers, according to the Ontario safety laws, have the right to refuse unsafe work and are responsible for working in compliance with the OHSA and the employer’s health and safety policies.
C) Workplace Committees and Representatives
The OHSA mandates the establishment of joint health and safety committees or the appointment of health and safety representatives in workplaces with a certain number of employees.
These committees or representatives play a role in:
- Identifying and resolving health and safety issues
- Promoting awareness
- Promoting education
For interactive and effective JHSC training, click here.
Employers and employees should familiarize themselves with the specific requirements of the OHSA and relevant regulations applicable to their industry. Regular training and compliance with the OHSA contribute to a safer and healthier working environment in Ontario.
2. Workplace Hazardous Materials Information System (WHMIS)
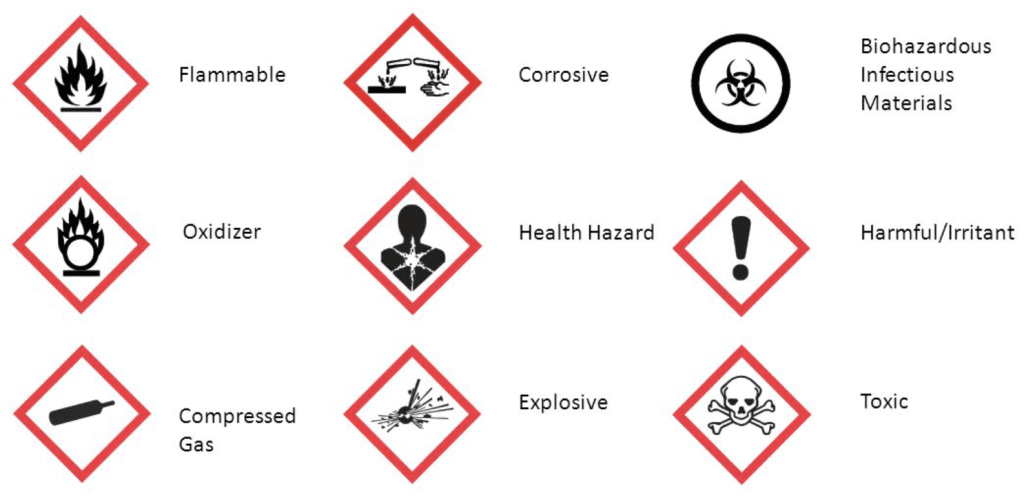
Learn how to safely handle hazardous products through WHMIS safety training.
WHMIS is a set of regulations that require employers to provide information about hazardous materials used in the workplace. It includes labelling, safety data sheets (SDS), and worker training.
A) Objective of WHMIS
WHMIS aims to protect the health and safety of workers by providing them with information about hazardous materials in the workplace.
The system ensures that workers are aware of the hazards associated with the materials they work with and that they have the knowledge to handle them safely.
B) Classification of Hazardous Materials
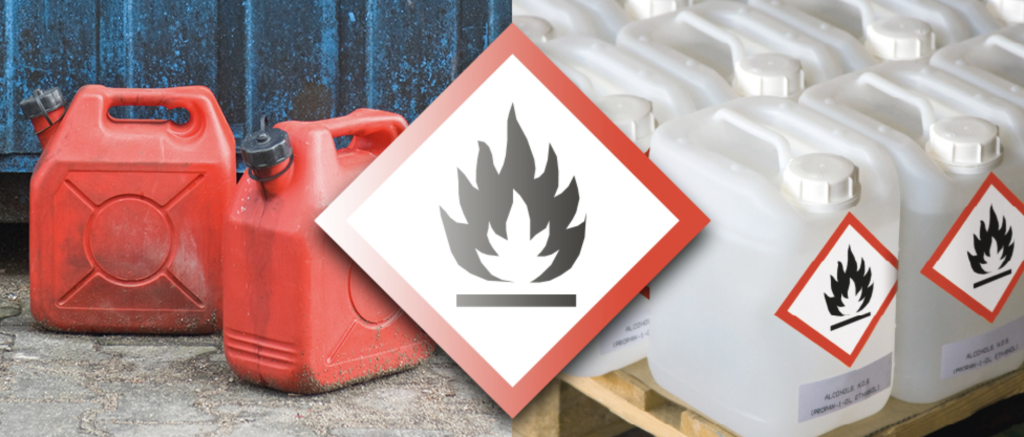
This icon lets you know that these liquids are flammable!
WHMIS classifies hazardous materials into different categories based on their physical and health hazards. These categories include:
- Flammable materials
- Corrosive substances
- Toxic materials
- And more
The classification system helps standardize the way hazards are communicated to workers.
For an explanation of each WHMIS symbol, check out our article “WHMIS Meaning: Icons Explained”.
C) Labels
According to Ontario safety laws, employers are required to label containers of hazardous materials in the workplace. Labels must include specific information such as:
- Product identifiers
- Hazard symbols
- Precautionary measures
Labels provide a quick visual reference for workers to identify the hazards associated with a particular substance and they save lives!
D) Safety Data Sheets (SDS)
Employers are required to obtain or create Safety Data Sheets (SDS) for each hazardous material used in the workplace.
SDS provide detailed information about:
- The properties of the hazardous material
- Its hazards
- Safe handling procedures
- Emergency measures
- And more
Workers have the right to access SDS to be informed about the materials they are working with. To understand how to read a Safety Data Sheet, read our article “SDS – How to Read”
In summary, WHMIS is a crucial component of occupational health and safety in Ontario, ensuring that workers have the information and training needed to handle hazardous materials safely. It involves a combination of labelling, documentation (MSDS/SDS), and comprehensive training programs to minimize the risks associated with workplace chemicals and substances. Employers, workers, and suppliers all play essential roles in the effective implementation of WHMIS.
3. Personal Protective Equipment (PPE)
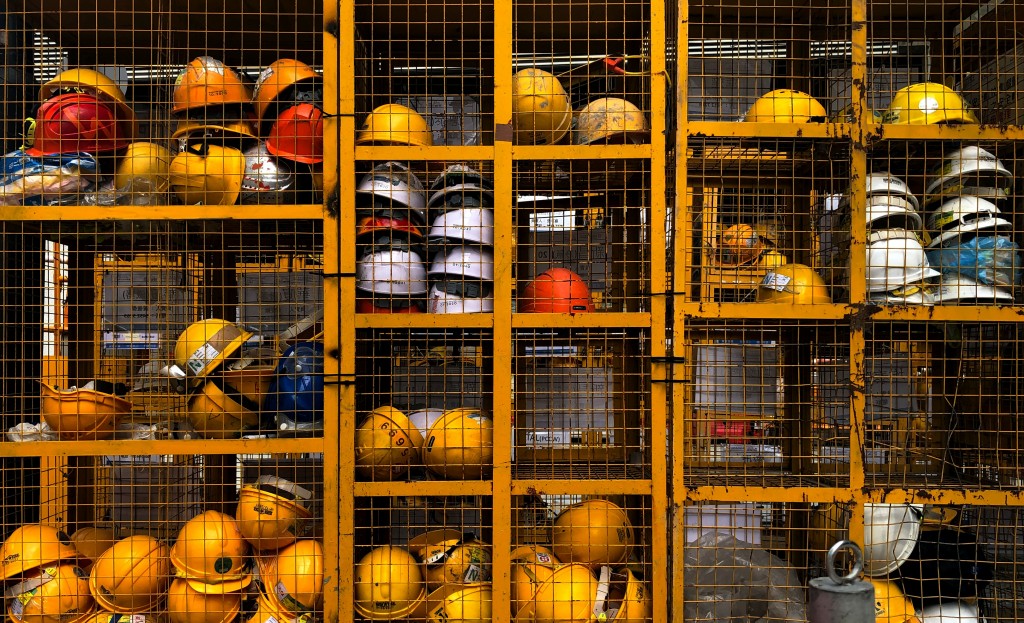
There are several Ontario safety laws regarding PPE.
Personal Protective Equipment (PPE) refers to specialized equipment or clothing worn by workers to protect them from specific workplace hazards.
In Ontario, as in many other jurisdictions, there are regulations in place regarding the use of PPE to ensure the safety and well-being of workers. Here’s a detailed explanation:
A) Hazard Assessment
Employers are required to conduct a hazard assessment to identify potential risks and hazards in the workplace. Based on this assessment, employers determine the types of PPE that are necessary to protect workers from specific dangers.
For example, if you employ welders, ensure that they are equipped with welding helmets to protect them from arc flash and radiation.
B) Selection and Provision of PPE
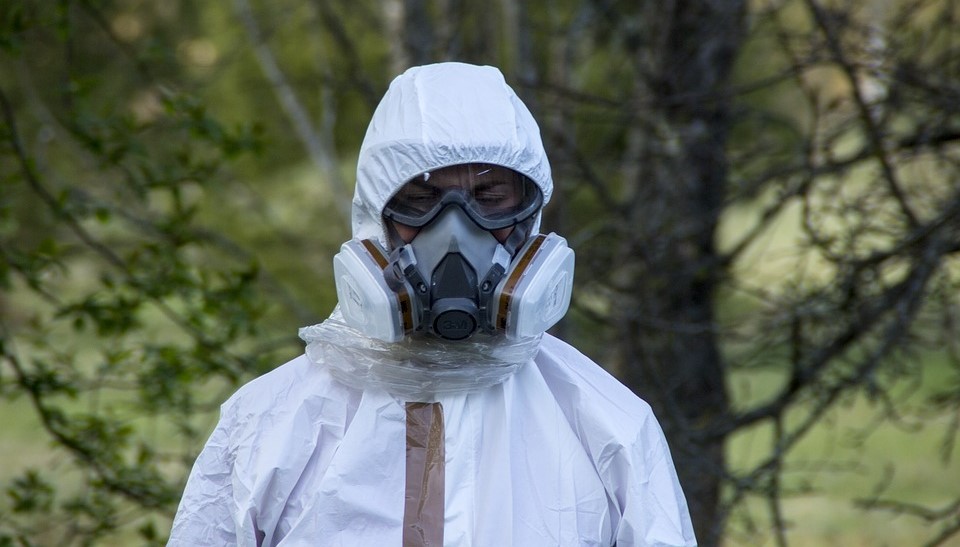
If you work in a hospital or as a paramedic, you are probably familiar with respirators.
Employers are responsible for selecting and providing appropriate PPE to employees free of charge.
PPE must be suitable for the specific hazards present in the workplace, and employers should ensure that it fits properly and is in good condition.
For example, in workplaces where there is a risk of respiratory hazards, regulations may detail the use of respiratory protective equipment, including masks or respirators. Therefore, employers must ensure that employees are properly trained on the use of respiratory protection and that the equipment is fit-tested when required.
C) Training and Instruction
Employers are required to provide training to workers on the PPE requirements. This training should include:
- Proper use
- Care
- Limitations
This training ensures that workers understand how to effectively use their PPE to minimize the risk of injury.
By regulating the use of PPE through Ontario safety laws, authorities aim to ensure that workers are adequately protected against workplace hazards. Both employers and workers need to be aware of these regulations, use PPE correctly, and actively participate in maintaining a safe work environment.
4. Specific Requirements
Some specific scenarios in the workplace require specialized training or equipment to ensure the safety of employees. Here are some examples:
A) Using Forklifts
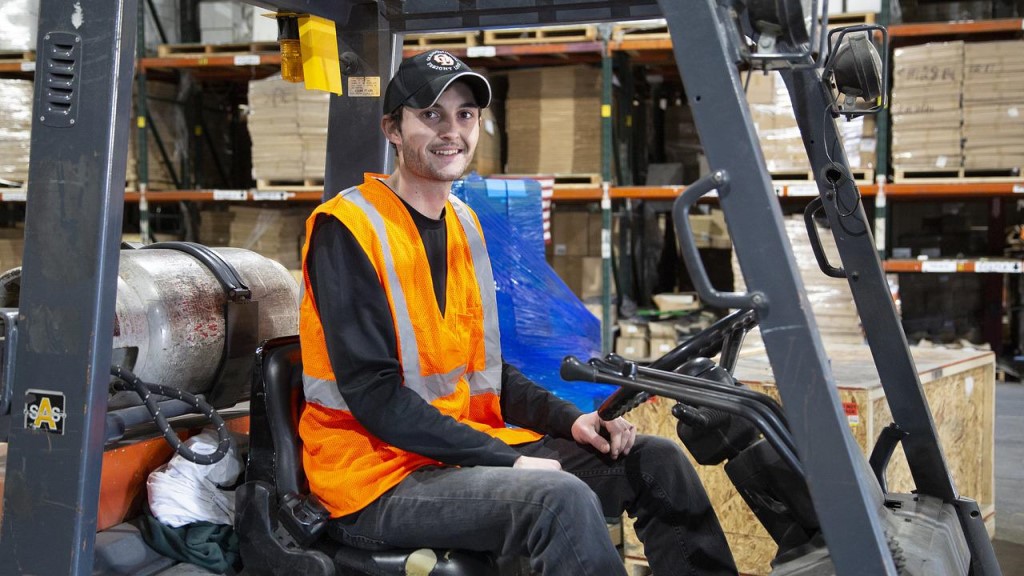
There are specific Ontario safety laws governing the use of forklifts.
- Training Certification: Operating a forklift requires specialized training to ensure the safe handling of the equipment and the protection of both the operator and those working around them.
- Certification Requires: Forklift operators typically need to obtain a certification in accordance with the relevant regulations, such as the requirements outlined in the Occupational Health and Safety Act (OHSA) and its regulations.
B) Working at Heights
- Training Certification: Employees who work at heights, such as on ladders, scaffolds, or elevated platforms, need specific training to prevent falls and other related hazards.
- Certification Required: According to Ontario safety laws, certifications in Fall Protection training and Working at Heights training are often required. The training may cover the proper use of fall protection equipment, the identification of potential fall hazards, and rescue procedures.
C) Working with Dangerous Materials
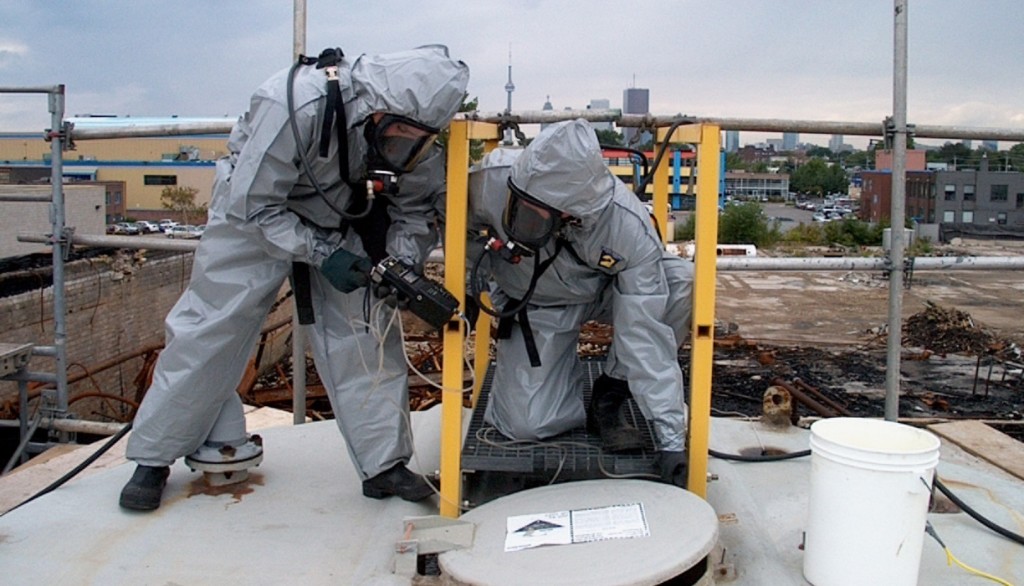
When working with hazardous materials, Ontario safety laws demand that you engage in HAZWOPER training.
- Training Certification: Employees handling hazardous materials must be trained in the safe storage, handling, and disposal of these materials. This includes understanding the properties of the materials and how to respond to spills or emergencies.
- Certification Required: HAZWOPER training and certification may be necessary. The specific certification requirements can vary based on the nature of the materials and the workplace.
D) Confined Space Entry
- Training Certification: Workers entering confined spaces, such as tanks or tunnels, require specific training to address the unique risks associated with confined spaces.
- Certification Required: Certification in Confined Space Entry training and Confined Space Rescue training and certification are often mandatory. This training covers the recognition of confined spaces, atmospheric monitoring, and rescue procedures.
E) First Aid and CPR
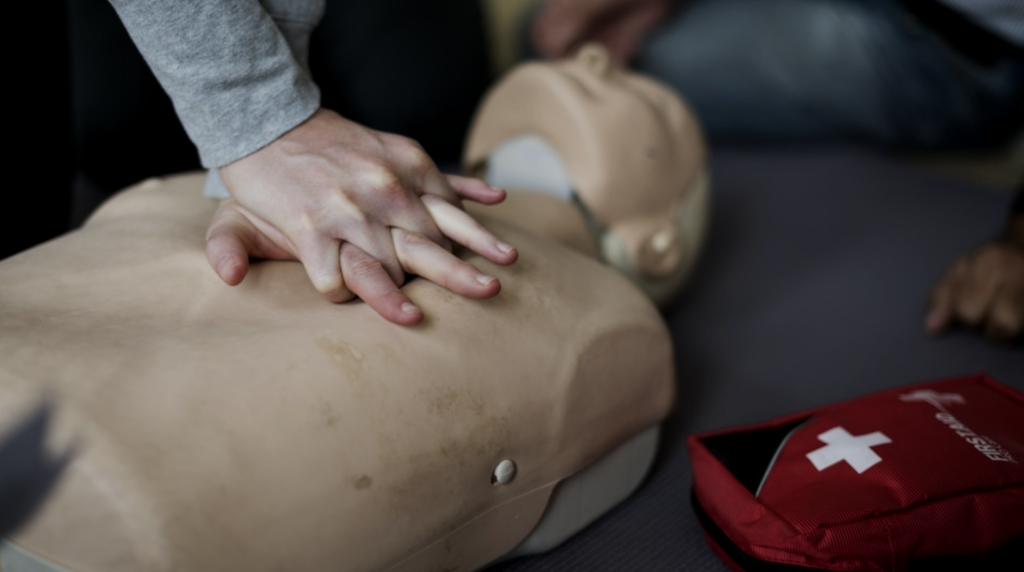
According to the Ontario safety laws, first aid and CPR is required for all first responders.
- Training Certification: Having employees trained in first aid and cardiopulmonary resuscitation (CPR) is crucial for providing immediate assistance in case of injuries or medical emergencies.
- Certification Required: First Aid and CPR certifications are typically provided by recognized organizations such as the Red Cross or the St. John Ambulance.
F) Lockout/Tagout Procedures
- Training Certification: Employees involved in servicing or maintaining equipment where the unexpected energization, start-up, or release of stored energy could cause injury must be trained in lockout/tagout procedures.
- Certification Required: Lockout/Tagout training and certification help ensure that employees understand how to control hazardous energy sources during maintenance activities.
Employers need to comply with relevant regulations and standards, and employees should undergo proper training to perform their tasks safely.
Certification requirements may vary based on jurisdiction and the specific industry. Employers should consult the applicable regulations and work with reputable training providers to ensure compliance.
Need Safety Training? Rely on ACUTE Environmental
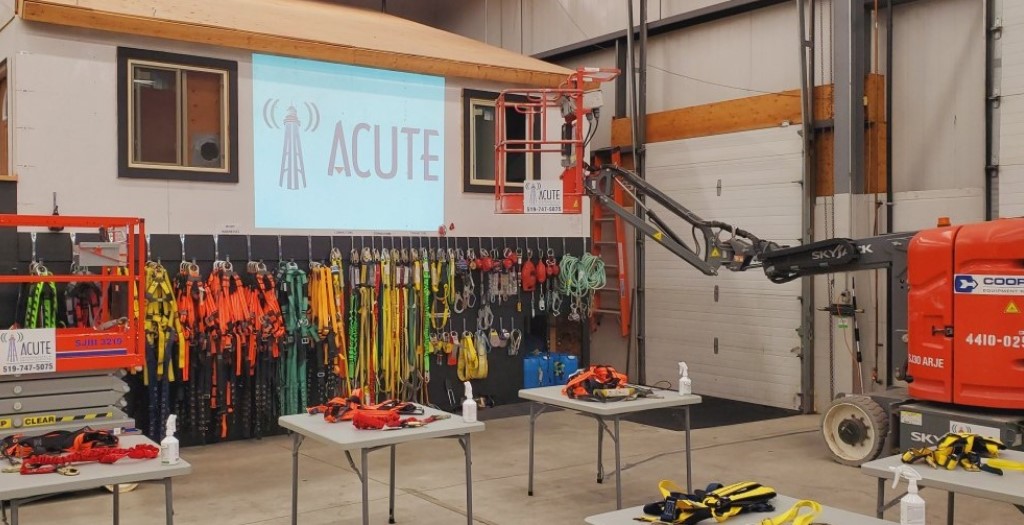
ACUTE can transform your workplace to be more safety-compliant.
If you have any questions regarding Ontario safety laws and/or you are concerned that your workplace is not safety complaint, book a course with ACUTE. Here are some of the benefits of working with ACUTE:
- Open Door Instructor-Student Partnership – ACUTE’s training services emphasize client participation, staff foster relationships with clients and serve as a touchstone for advice anytime moving forward.
- Serving Your Team and Industry – With a vast array of clients in manufacturing, construction, health, academic, and government sectors, ACUTE brings the best safety practices from across the spectrum to your workplace.
- 100 Years Combined Experience – ACUTE provides comprehensive health and safety training, on-site safety services, and consulting services. With over 100 years of combined experience, our company staff offers more than theoretical or abstract ideas. ACUTE offers solutions!
- Track Record of Success – ACUTE is rated 4.9/5 stars on Google reviews, demonstrating our commitment to our clients, our quality, and our passion for training.
It is one thing to understand what HSE is and another to know how to conduct an HSE presentation. Contact Acute Environmental today to learn more about health, safety, and the environment.
What Our Customers Are Saying…
We were referred to ACUTE on behalf of our employer for an n95 mask fitting – the staff here are professional, personable, and informative.
I’d come back here for any safety-related training in a heartbeat.
Acute has been a staple in supporting my companies over the years and have always delivered quality and dependable service. Training programs are top shelf and a great facility for practical application. couldn’t recommend them more. keep up the great work folks.
Outstanding service provided by Acute, right from the customer support end, right through to the delivery of the session. Always professional, quick to respond, and always delivering services that exceed my expectations. Acute has an amazing team that is always helping us achieve better health and safety performance. So are grateful to have such a tremendous resource in Acute!
Hours of Operation and Contact Information:
Monday-Friday: 8:00 AM – 5:00 PM
Saturday-Sunday: Closed
Phone: (519) 747-5075
Fax: (519) 747-4608
Email: info@acuteservices.com