Working with risks and hazards is an unavoidable reality for many workplaces. Getting trained to conduct a proper risk assessment can mean the difference between avoiding and experiencing injury or even fatality. ACUTE offers the best and most hands-on training for hazard assessments for Joint Health and Safety Committee members, to help keep your team on a secure foundation.
Issues with Not Doing a Hazards Assessment
Employers must be aware of the potential hazards in the workplace so that their team can be adequately trained to avoid loss of working time, productivity, and damaged public reputation. Without proper awareness concerning the many hazards faced by your team, a number of safety risks will arise. Here we identify hazards such as workplace objects, chemicals, or tools that could cause harm, and define risk as the probability or likelihood of those hazards causing that harm. The following video illustrates the difference and provides an introduction to hazard assessment:
A number of issues arise when an organization fails to engage in a hazards assessment.
Responsibility of Employers
There are a number of stipulations mandated by the Ministry of Labour, Immigration, Training and Skills Development in the Ontario Health and Safety Act (OHSA). A Joint Health and Safety Committee (JHSC) is recommended to ensure the effective planning, implementation, and renewal of hazard controls in the workplace. Employers are required by OHSA to:
- Take every precaution necessary – to safeguard their staff, including the assessment and control of workplace hazards (i.e. hazardous materials, workplace violence, confined spaces, etc).
- Reassess regularly workplace hazards – to ensure that the safety policy or program remains effective (it is recommended that organizations do so annually, at minimum).
- Ensure a trained or experienced individual conducts assessment – the ministry requires that hazards assessment must be conducted by a qualified and trained individual.
- Communicate and train employees – in order to help them work safely, cognizant of the risks and hazards around them.
- Provide training and instructor meeting MLITSD standards – employers are to provide approved training to safeguard their staff.
- Get Certified JHSC Members – often times the ministry requires a minimum of 1 or more JHSC members to be certified. See here for more details.
Please ensure a full review of the OHSA is conducted. The content posted in this blog is meant to inform generally, rather than act as a comprehensive guide on ministry regulations.
What is a Hazards Assessment?
A hazard assessment entails (required by law) identification of the hazards associated with the work assigned to staff, prescribing personal protective equipment and protection measures which must be used to reduce the risks posed by these hazards. A hazards assessment helps you to look at the big picture when your team faces the perils of the job site or workplace. Its chief goal is to ensure good practices are in place to protect employees. An assessment further includes evaluating where working with hazards is absolutely necessary, identifies workplace or task risks, and establishes processes/standards to protect those exposed to hazards.
Conducting a hazards assessment supports everyone in a workplace in the following ways:
- Provides awareness of the environmental, interpersonal, and personal hazards faced by each member of the team.
- Helps manage the probability of risk from hazards.
- Establishes procedures and safety guidelines.
- Provides greater protection against regulatory sanctions as a result of safety negligence.
- Provides peace of mind for staff.
How to Tell if a Hazard Assessment is Needed
If you or your team continue to experience these signs, contact ACUTE today to ensure you stay above risk.
- Regular close calls – if you continue to hear stories of near incidents, this indicates that your team, process, or equipment may be exposed to risk.
- Inconsistent application or understanding of procedures – there is a lack of clarity in how to use equipment or conduct work safety setup.
- Complaints of Being Exposed to Hazards – when employees express concerns about safety the JHSC must act quickly to address the risk.
What are Types of Workplace Hazards?
A credible source provides this list of common workplace hazards to help safety planners evaluate their workplace:
- Biological – bacteria, viruses, insects, plants, birds, animals, humans, etc.
- Chemical – the physical and toxic properties of the chemical.
- Ergonomic – repetitive movements, improper set-up of workstations, etc.
- Physical – radiation, magnetic fields, pressure extremes (high pressure or vacuum), noise, etc.
- Psychosocial – stress, violence, etc.
- Safety – slipping/tripping hazards, inappropriate machine guarding, equipment malfunctions, and breakdowns.
What are the Steps in a Working at Heights Risk Assessment?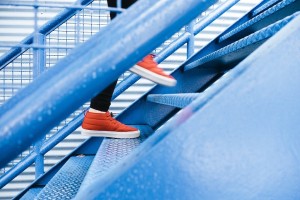
Here are steps to conducting a WAH risk assessment along with ensuring its relevancy as your business changes. The Health and Safety Executive offers these guidelines which have been adapted for WAH:
1 – Evaluate Work that Must be Conducted Amidst Hazard
- Analyze where working at heights is not necessary.
- Resolve to reduce the hazards at which work is done.
- Utilize remote technology, as some tasks may be completed using drones or using automated machinery.
2 – Identify the Hazards and their Risk Profile
- For each procedure, identify and outline the hazards including chemicals, electricity, equipment, ladders.
- Alongside the people who do the job, determine how hazards independently or in conjunction can cause harm.
- Document your findings and scenarios for further analysis.
3 – Decide who Might be Harmed and How
- Determine the individuals or objects that could be harmed in the scenarios identified.
- Understand the nature and extent of harm that may occur.
If you need help conducting a working at heights risk assessment, contact us here or see what others have said about ACUTE’s services:
“Very professional approach to consulting. I am not surprised about the success ACUTE has achieved over the last 15 years that I have worked with them.“
–Konstantinos Varas, ACUTE valued client
See here for more testimonials.
4- Evaluate the Risks and Decide on Precautions
- Analyze the likelihood of hazards which could cause harm to an individual.
- Identify and rank each of the probable incidents.
- Determine measures to mitigate risks. This includes identifying clear setup procedures, check-in, and take-down steps.
5- Record Findings
For each finding determine next steps for:
- Workplace training.
- Workplace procedures.
- Workplace communications.
6- Review Your Assessment and Update if Necessary
- Review findings and update your risk assessment periodically.
- Invite open dialogue on what continues to pose challenges, and celebrate achievements that continue to help your team remain safe.
- Monitor safety outcomes like the number of incidents per quarter or other metrics can help you identify when a risk assessment should be conducted again.
Conducting a hazard assessment is an on-going process not limited to JHSC members. For those who are looking to get started now, here is a document that can serve as an example or template for organizations interested in understanding more.
A Checklist for Hazard Assessment
Here are highlights of a more comprehensive checklist (linked below) of areas of focus for any safety planner looking to get a jump start on hazard identification.
- General work environment
- Personal protective equipment
- Walkways
- Floors, walls, and stairways
- Elevated surfaces
- Exit doors
- Machine guarding
Ensuring your team gets the right joint health and safety committee training is not just about using a checklist but making an organizational impact by improving the safety culture of your team. The full listing for this checklist resource can be found here.
Getting Joint Health and Safety Committee Training Improves Quality of a Hazard Assessment
Conducting the most comprehensive and in-depth hazards assessment requires that your safety planners are aware of the unexpected hazards of your workplace. Training is the best way to ensure your team is prepared to handle existing and unforeseen challenges. See our previous article to help you understand the wide array of requirements and certification processes for joint health and safety committee training.
Benefits of Choosing ACUTE training to get the best hazard assessments:
- Our trainers have first-hand experience in identifying and managing hazards.
- Wide-range knowledge of managing and controlling hazards across a variety of industries.
- Depth of safety equipment knowledge and ability to refer the right equipment for the right situation.
- Our training programs are tailored to your specific industry, facility, and company policies and procedures.
- Our training can be made available on-site or at our first-class Training Centre.
- We work to provide the best customer service in the industry to our clients.
ACUTE offers two courses in regards to helping JHSC members conduct hazard assessments. In order to qualify for hazards assessments and to receive JHSC certification, both Basic and Advanced competency must be achieved.
Part 1 Basic Training for JHSC Certification (The Basics) – CPO Approved
This 3-day certification course provides in-depth training on the health and safety law, hazard recognition, risk assessment, hazard control, accident and incident investigation techniques, and an overview of prevention resources. The course is Cheif Prevention Officer approved (CPO approved). Upon completing the course, you will still need to complete part 2 of the training to receive a JH&SC certification. Any company that regularly employs 20 or more workers is required to create a Joint Health and Safety Committee.
Duration: 3 days (24 hours)
Part 2 Basic Training for JHSC Certification (Identifying Hazards)
To take part in this process you need to have completed Part 1 Basic Training for JHSC Certification. In this course, you will learn how to identify and develop a plan to control significant safety hazards specific to your workplace. Part 2 is required to receive your certification and status card. This training must be completed within 1 year of part 1 of the training to be valid.
Duration: 2 days (13 hours)
Prerequisite: Part 1 Basic Training for JHSC Certification (The Basics)
ACUTE Guides Your Team in Conducting a Hazard Assessment
A hazards assessment can take anywhere from approximately 2 months to a year depending on industry and resource commitments. The challenge is that often times hazards are missed or proper scenarios may not be identified without the proper training or consultation by a qualified subject matter expert. If you are interested in having ACUTE come and help you conduct a hazard assessment, or train your team on how to do a thorough assessment feel free to contact us.
ACUTE is located in Waterloo, Ontario and services customers from the cities such as Toronto, Mississauga, Brampton, Hamilton, Milton, Kitchener, London, Guelph and many other cities from across Ontario and North America.